The properties of CC composites are dominated by the reinforcements used and their physical properties, which result from the processing selected and woven preform configuration. In almost all circumstances, physical strength characteristics of the fibers used are reduced as a result of their handing during weaving and the severe environment of densification. Therefore, prediction of composite characteristics typically uses selected test coupon values to establish basic characteristics.
Figure 17 indicates that CC composite properties consisting of tensile strength, modulus, strain, and property value are retained as a function of test temperature and fiber volume fraction. These typical composite data are developed based on PAN precursor fibers used in a 3D orthogonal construction in which the fibers exhibit a tensile modulus of nominally 50Msi and tensile strength of nominally 400 ksi prior to weaving and densification. The fiber values referred to for tensile and modulus properties are in the direction of interest. For example, a 100 percent fiber volume references a unidirectional (1D) composite that has a fiber fraction of typically 50 percent. When considering a 3D orthogonal CC composite, a Z-direction fiber volume of 40 percent is typical, with a resulting fiber fraction of under 20 percent when considering that total fiber fraction of the composite is less than 50 percent. Therefore, the predicted tensile strength would be nominally 50 ksi to 60 ksi. One of unique characteristics of CC composites, similar to monolithic graphite, is the increase in strength properties with increasing temperature to approximately 4000C. cfccarbon.com
The predictions of properties indicated in figure 17 are intended to act as a guideline. Significant variations may be obtained by both the selection of reinforcement and, to some extent, the densification process.
In summary, CC composites may be fabricated for a variety of constructions ranging from unidirectionally reinforced composites to n-directions of reinforcement. Selection of the woven configurations is mandated by final application and associated costs. Manufacturing processes such as braiding, filament winding, polar coordinate weaving, chopped fiber casting, involute, fabric weaving, and multidirectional weaving have all been successfully applied. The associated densification processes of CVD, resin/pitch impregnation, or combinations are again selected for the requirements of the applications. The basic methods of preform fabrication and densification have been described to indicate the techniques developed over the past 20 years. Numerous variations of these processes are applicable. Selection of the appropriate approaches (reinforcement, preform fabrication, and densification) is dependent on the desired composite properties and intended environment of the composite applications.
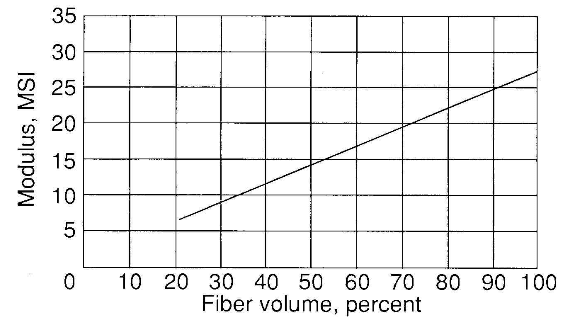
17-a-modulus as function of fiber volume in direction of applied load
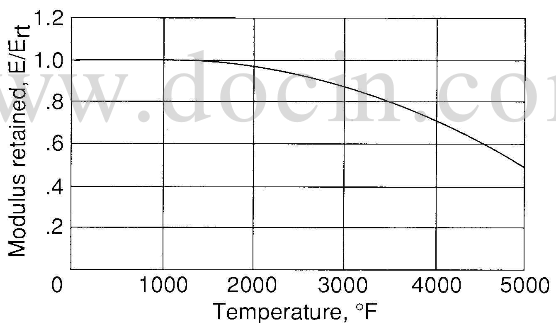
17-b-retention ratio of modulus as function of temperature
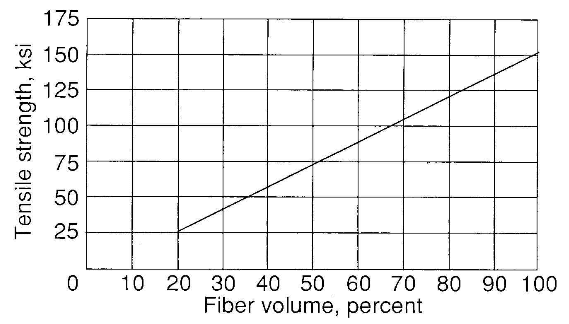
17-c-tensile strength as function of fiber volume in direction of applied load
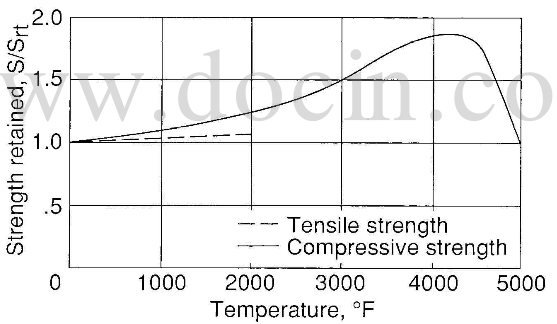
17-d-tensile strength as function of fiber volume in direction of temperature