Table 15.4 lists the most common ceramics used for composite ceramic materials.
A ceramic matrix will provide improved mechanical properties if nanosize (<100nm) material is added, particles of which are so small that they can be trapped at the grain boundaries or within the grains.
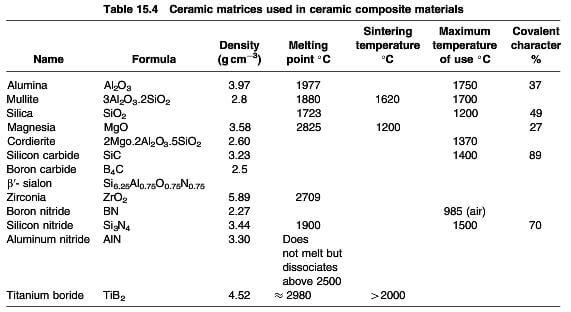
ceramic matrices used in ceramic composite materials
Oxide matrix materials:
- Alumina (Al2O3)
Alumina has a high melting point and is a widely used ceramic, but it does have a high expansion coefficient. When deposited via the sol gel
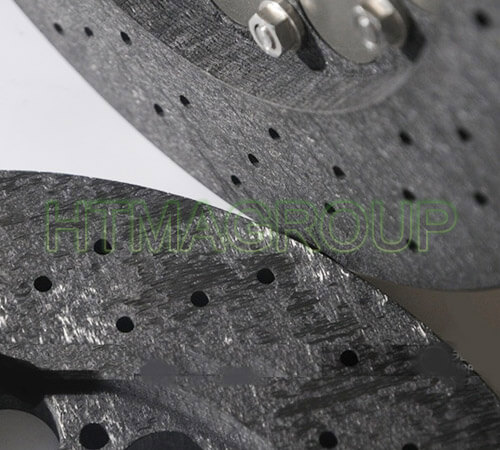
carbon ceramic composite
method, excessive shrinkage occurs on drying and firing, which has to be counteracted by the addition of Al2O3.
The following reaction with carbon can occur:
9C+2Al2O3→Al4C3+6CO
And is best prevented by coating the carbon fiber with SiC.
- Mullite (3Al2O3.2SiO2)
Mullite has a slightly lower melting point than alumina, but the expansion coefficient is low and similar to SiC.
- Zirconia (ZrO2)
Zirconia can be used with Al2O3 to form a series of particulate reinforced composites, with the zirconia particles intergranularly dispersed within the alumina and the composite benefiting by strength retention for many hours at 1000C. With ZrO2 rich dispersions, the Al2O3 increases strength at room and elevated temperatures and also increases the fracture toughness.
Non-oxide matrix materials
- Silicon carbide (SiC)
Silicon carbide shows great promise as a matrix material, retaining strength up to 1400C, but unfortunately, it does exhibit brittle behavior up to 2000C. Carbon fiber has been used for the reinforcement of SiC. The thermal shock resistance is also improved if carbon fiber is used as reinforcement. However, the carbon fiber must be coated to confer a measure of protection against oxidation.
Ansorge produced a carbon fiber reinforced SiC ceramic matrix composite by liquid phase infiltration of Si into a carbon-carbon composite.
Resin transfer molding can be used to produce near net shape ceramic matrix composites, followed by pyrolysis.
- Titanium carbide (TiC)
Titanium carbide can be added to SiC to improve strength and fracture toughness.
- Boron carbide (B4C)
This material is almost as hard as diamond and has to be fabricated by hot pressing. The B4C will, however, inhibit the grain growth.
- Titanium boride (TiB2)
Tianium boride has a particle size about 8um and can be hot pressed at temperatures >1800C in a vacuum or 1900C in Ar, to give almost theoretical density. Sintering aids include C, Fe, Co, Ni, W and WC. For hot isostatic pressing at temperatures >2000C, sintering aids can include Fe, C/Cr, Cr3C2. Titanium boride can be reinforced with ZrO2 to improve the strength and toughness.
- Boron nitride (BN)
Boron nitride may be added to Si3N4 to improve shock and electrical resistance. BN is covalently bonded and resistant to sintering without the addition of liquid forming additives, such as Si3N4, SiO2, Y2O3 and CaO, which will allow sintering between 1600-1900C.
- Aluminum nitride (AlN)
Thermal conductivity is eight time higher than Al2O3 and second only to beryllia. The thermal expansion matches Si and at 200C, exceeds that of Cu.
A reaction with carbon can occur:
3D+4AlN→Al4C3+2N2
And is best prevented by coating the carbon fiber with SiC.
- Silicon nitride (Si3N4)
It exceeds other ceramics in thermal shock resistance and strength is retained at elevated temperature. If can be sintered, reaction bonded or hot pressed.
Silicon nitride has been reinforced by carbon and Suzuke et al have investigated fiber pullout mechanisms of carbon fiber reinforced Si3N4 ceramic composites. Carbon fiber composites are stable in N2 at high temperatures. At present, interest have been generated in SiC-SiC composites. Lundberg et al successfully HIPed carbon fiber reinforced Si3N4 composites and Guo et al used carbon fiber to reinforce Si3N4.
Silicon nitride will react with carbon:
3C+Si3N4→3SiC+2N2
And is best prevented by coating the carbon fiber.
related news /articles:
Liquid phase infiltration of CC composites (2)—thermoset resin matrices
Liquid phase infiltration of CC composites– Pitch matrices
Carbon fiber reinforced silicon carbide composites (C/SiC, C/C-SiC)-(1)
Ceramic matrix composite (CMC) material | professional manufacturer in China