A clear manifestation of development of distortion of geometrical shape of a carbon object is seen from Fig.1. A fragment of a thin-walled large conical billet is presented after HTT. The billet in a stage of carbon-reinforced plastic processing is prepared by winding cloth strips. With winding over a geodesic line as there is a change in billet diameter there is also a change in winding angle. Here within the limits of an area of surface of not more than 300 mm there is rotation of directon of the cloth warp (X) and correspondingly the cloth weft (Y) by more than 45°. Attention is drawn to the form of deformation development of an area of billet. In the direction of the billet material warp it ther was an increase in length, and in the weft direction twisted corrugations formed. Elongation of individual billet directions leads to a change in its overall dimensions.
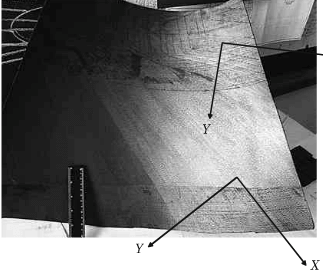
fig.1-fragment of thin-walled large component deformed as a result of HTT
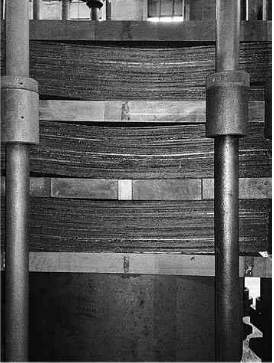
fig.2-charge of deformable carbon-carbon plates in an electric vacuum furnace in the HTT operation stage
Shrinkage is shown in Fig.2 for a plate with thickness up to 6 mm of carbon-carbon composite after HTT in an electric vacuum furnace. Plates for treatment were placed on a graphite platform. To the left and right in the field of view there are cylinderical graphite heaters 60mm in diameter. As may be seen, plates after completion of the operation are deformed with a sag of more than 30 mm. In spite of the significant hegith of a charge, and obviously its weight, the lower plates have more marked shape changes.

fig.3-change in billet diameter during production operation
Results are presented in Fig.3 for a change in shape in the greatest diameter of a closed conical billet in individual stages of its manufacture. The change in billet diameter was calculated as the rati ofdifference in greatest and least diametes in the section to the average size. Wall thickness was 10-12mm. The nominal diameter of a billet in the measurement zone was 2250mm. Billets of this production series in the stage of carbon-reinforced plastic producti processing were prepared by winding ribbon of high-modulus polyacrylonitrile carbon thread, followed by autoclave hardening. Deviation in carbon-reinforced plastic billet from the nominal diameter has a mean statistical character with expectation of the average value around zero deviations from the nominal value. The averge value of carbon-reinforced plastic diameter for a billet almost equals the diameter of the metal mandrel, on which billet shaping is carried out. After completion of carbonization of observed average deviation of diameter from the nominal becomes positive. This means that the nominal value of the average diameter increased. In the HTT stage the change in billet shape is considerable as there is an increase in the maximum temperature of the process starting from 1900°C. Possible practical application of an object is government by its purpose and tolerances of the design documentation. In order to keep shape change to a minimum level it is apparently necessary to develop special production measures.