Advanced thermal protection materials envisioned for us on future hypersonic vehicles will likely be subjected to temperatures in excess of 1811 K and, therefore, will require the rapid conduction of heat away from the stagnation regions of wing leading edges, the nose cap area, and from engine inlet and exhaust areas. Carbon-carbon composite materials are lightweight, retain their strength at high temperatures, and have high and tailor-able thermal conductivity. These characteristics make them attractive candidates as advanced thermal system materials.
Carbon-carbon composites comprise a family of materials having a carbon matrix reinforced with carbon fibers. A large variety of both fibers and matrix precursor materials is used. The choice of precursor materials and the thermal processing used to fabricate the composites are major factors which determine the thermophysical properties of the materials. Availability of this information enables the user to better utilize the thermophysical property data and allows for more meaningful comparisons between data sets. A search of the literature found little thermal conductivity data for C-C materials above 1225K. In some instances, thermal conductivity data were reported, but an adequate description of the precursor materials and the thermal processing history was not reported.
Because a need was recognized for in-plane and through-the-thickness thermal conductivity data for C-C composite materials over a wide temperature range, Langley Research Center (LaRC) embarked on an effort to compile a consistent set of thermal conductivity values from room temperature to 1992K for C-C composite materials on hand at LaRC for which the precursor materials and thermal processing history were known. This report documents the thermal conductivity data generated for these materials.
Experimental procedures:
Table 1 gives a description of the 28 materials for which thermal diffusivity measurements were made and reported in this report. All the materials were derived from previous studies aimed at improving mechanical properties and/or oxidation resistance. Material specimens 1 through 10 and 16 through 18 were fabricated to investigate the effects of different reinforcements and different densification techniques on mechanical properties. Material specimens 11 through 15 were fabricated to explore the benefits of candidate substrate oxidation inhibitors and coating types. Material specimens 19 through 26 were fabricated to investigate the effects of chemical vapor infiltration processing parameters on the thermal conductivity and mechanical properties of carbon-carbon composites. Material specimens 27 and 28 were fabricated as candidate materials for a thermal shield on a proposed NASA solar probe spacecraft.
The source of each material is in the second column of table 1. The fiber type and tow size are in the third column. Most of the materials were made with T-300 fiber. Two materials were made with T-50 fiber, four were made with Celanese celion fiber, and two were made with K321 fiber. All specimens except the four that were made with Celion fibers were constructed using an 8 harness satin weave(8HSW) fabric. The number of tows per inch in both the warp and fill direction is given. Material specimens 16,17, and 18 are stitched panels. The weave construction for the materials made with the Celion fiber were 3D orthogonal. The layup for all materials except those made with the Celion fiber was 0/90°, and most of them were 7- or 8-ply laminates.
Table 1: 28pcs of C/C composite specimens:
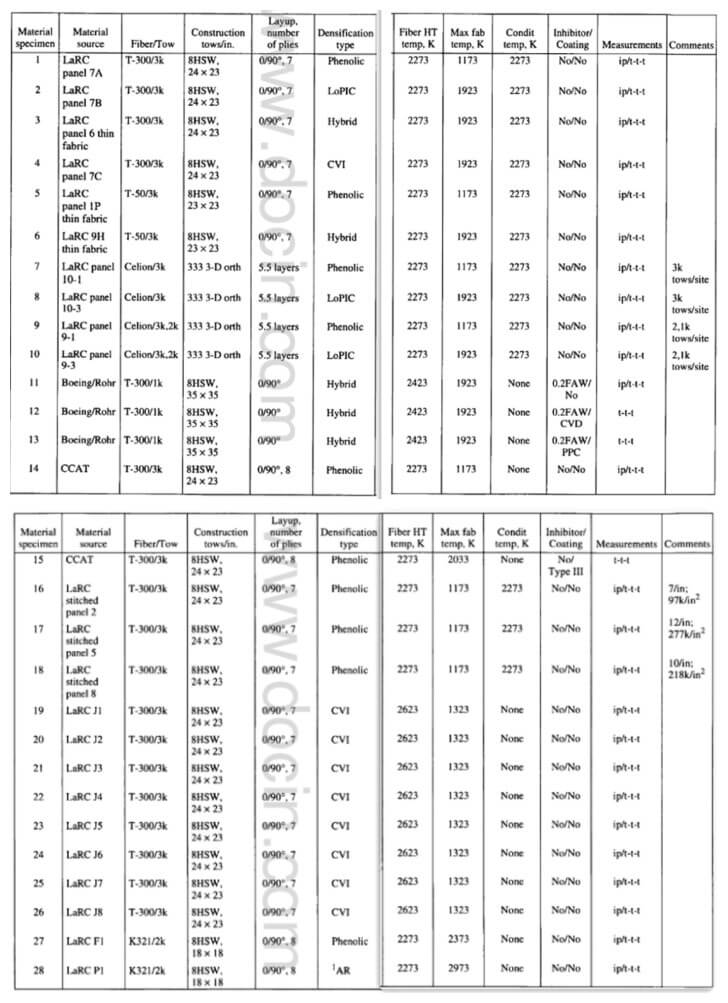
table 1-28pcs of c/c composite specimens