Ideally, a barrier coating should adhere well to the carbon fiber composite and be free of cracks, with a coefficient of thermal expansion close to the value for the substrate. The coating should have good high temperature resistance and prevent O2 ingress and C egress. Barrier coatings include noble metals, carbides, borides, nitrides and SiC.
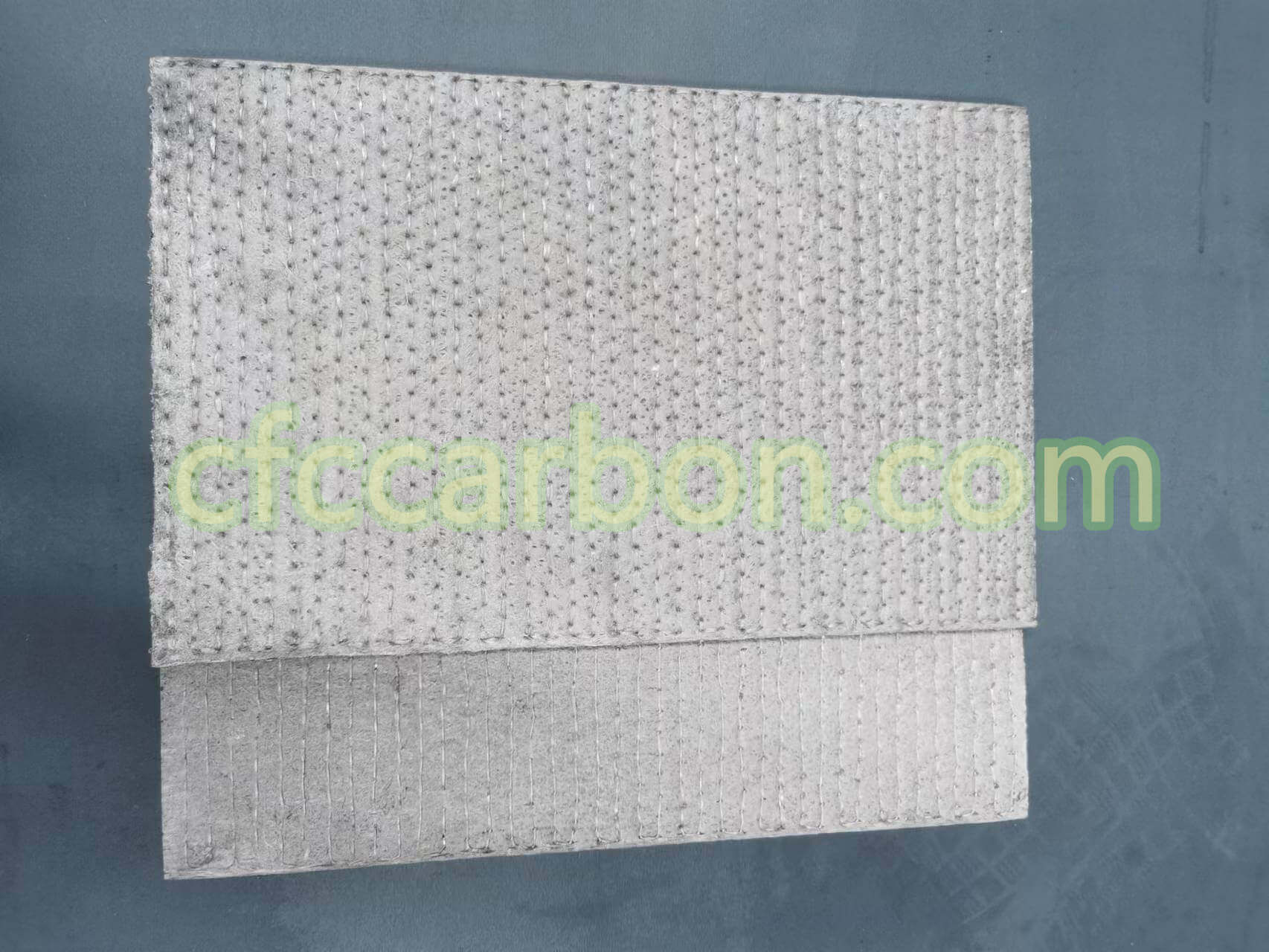
SiC coating carbon fiber composite material-CC-CFC (1)
- Noble metals
Iridium (mp=2440C) does not react with C to form carbides (up to 2280C) and is a superb barrier to O2 (up to 2100C) but is very expensive and difficult to apply with poor adhesion to carbon composite. At high temperatures, it can form volatile Ir2O3 and IrO3, which can cause erosion.
- Silicon coatings
Pack cementation, or SiC conversion, can be employed, where the materials to be coated are packed in containers holding Si, SiC, Al2O3 and MgO powders. These react at 1600C to form a SiC coating graded from pure carbon on the inside to pure silicon on the outside and achieving a thickness of about 0.5mm.
Si (l or g)+ C→ SiC
SiO+2C→SiC+CO (g)
Molten silicon does, however, have a preference to react with the carbon fibers rather than with the carbon matrix and this can be avoided by applying an initial coat of SiC using the CVD process, giving a more dense coating.
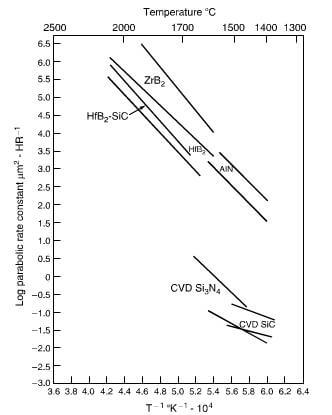
Oxidation characteristics of high temperature ceramics
Chemical vapor deposition using CH3SiCl, or CH3SiCl3 in the presence of H2 at 1125C can employed to deposit an outer coating of SiC from the gaseous phase, which acts as a primary barrier to O2 ingress. A B rich inner layer, applied by slurry coating, or the CVD process, provides the means of sealing any cracks in the outer coating.
There is a good thermal expansion match with carbon-carbon composites and silicon ceramics. SiC is limited to use at 1700C as the layer is disrupted by formation of CO.
At temperatures below 1150C, the viscosity of the silica glass is too high and is it unable to flow into any cracks that may develop. However, it is widely used in conjunction with B.
An alternative approach is to use a carbon-silicon matrix via chemical vapor infiltration with carbon and SiC co-deposition from CH3SiCl3, C2H2, Ar and H2, by gradually varying the source gases in semi-continuous process, from C2H2 to CH3SiCl3. Although this material seems to be macroscopically homogeneous, microscopic examination shows a gradient variation of the matrix sheaths around each fiber. The oxidation resistance of the material is significantly superior to that of a carbon-carbon material.
A serious problem with a SiC coating is spallation and crack formation due to thermal mismatch stresses. Applying a graded coating-pure carbon on the inside and pure SiC coating on the outside-helps to minimize spallation.
General Atomic technologies have developed another process termed a preceramic polymer coating (PPC) using a polymeric coating system made by Ethyl Corporation, which have been shown to perform as well as, or better than, the industry standard CVD-SiC system.
Carbon-carbon made with a cellulose based carbon fiber has a coefficient of thermal expansion about twice that a a PAN based carbon fiber system. Since the cellulose based carbon-carbon has a CTE fairly close to that of SiC or Si3N4, it is consequently less of a mismatch than a PAN based system, it will be necessary to accommodate this serous mismatch of CTEs and will require a sustained program of research to find a solution.
Silica films can be used as O2 diffusion barriers and may be applied by impregnation with tetraethylsilicate (TEOS) or by a sol-gel process. Extended use of silica coatings above 1200C is restricted by recrystallization occurring, with subsequent shrinkage and cracking. SiO2 has relatively poor wetting characteristics and at high temperatures, SiO2 must be separated by a hard oxide from the carbon-carbon, as other wise, it is reduced.
related news /articles:
Advanced Oxidation Protection Strategies for Carbon-Carbon Composites
Coating systems for carbon fiber carbon composites material (1)
Introduction of high-temperature coatings on CC composite material
Advanced Protective Coatings for Carbon-Carbon Composites