The tensile fracture stress and strain of carbon fiber-reinforced carbon matrix composites (C-Cs) were examined as functions of the bulk density. When the density increased, the interfacial strength of the C-Cs monotonically increased, and the tensile fracture strain decreased. In contrast, the tensile fracture stress was improved and degraded in the regions of density lower and higher than 1.6g/cm3, respectively. Two tensile fracture mechanisms of the examined C-Cs were identified with the transition at the density of 1.6g/cm3. In the low-density region, load transfer capability across fiber-matrix interfaces was shown to have an important role, and in the high-density region, stress concentrations at matrix-crack tips were presumed to be a major factor for the tensile fracture of C-Cs. This suggests that the most important interfacial property for tensile fracture is not interfacial sliding but debonding stress.
The tensile strengths of carbon fiber reinforced carbon matrix composites are usually much lower than those expected from the rule of mixture. In order to identify the mechanisms yielding such low strength, the effects of various potential factors including the heat treatment temperature, the fiber-matrix interfacial strength, and defects in the C-Cs have been studied. However, to the best of the authors’ knowledge, clear understanding of this phenomenon has not been attained. Continuous fiber-reinforced ceramic matrix composites (CFCCs) also elongate to a much lesser degree than the reinforcing fibers. Statistical models have been proposed to explain the tensile strength of CFCCs, in which the fiber-matrix interfacial property has had predominant influence on the ultimate tensile fracture strain. C-Cs improved with the weakening of the interfacial bonding. However, the mechanisms of the tensile fracture of C-Cs have remained unclear.
The present authors previously examined the effect of density on the tensile strength of various C-Cs, and the tensile strength of the C-Cs was reckoned to decrease with increasing the matrix-fiber interfacial strength, where the interfacial bonding enhanced with increase in C-C density. However, this result contradicts most of the previous studies; the tensile strength of C-Cs is usually reported to increase with density. To resolve this contradiction, the tensile strength of C-Cs is examined carefully in the present paper, particularly focusing on the fracture behavior of low density C-Cs. The fiber-matrix interfacial strength in C-Cs has been indirectly estimated in previous studies, for example, by observing pull-out length of fibers on the tensile fracture surface. In contrast, in the present study, both the strength of the fiber-matrix interface and the distribution of the fiber strength were determined in order to precisely understand a role of the interface in the fracture process. Three-dimensionally reinforced (3D) C-C have been reported to possess lower fiber-matrix interface than two-dimensionally reinforced (2D) C-Cs. The present authors paid attention to the results and, in order to examine the role of the interface clearly, C-Cs composed of the same constituent materials and processing route but possessing different reinforcing pattern, 2D and 3D C-Cs, were prepared. Then, the fracture behaviors of these C-Cs are compared. Finally, using these experimental results, tensile fracture models, being successful for CFCCs, are applied to the C/Cs for the discussion concerning dominant tensile fracture mechanisms.
Materials:
Cross-ply lamination (2D) C-Cs are mainly used in the present study; these C-Cs are reinforced with a high-strength carbon fiber. The fabrication process of these C-Cs is illustrated in fig1.
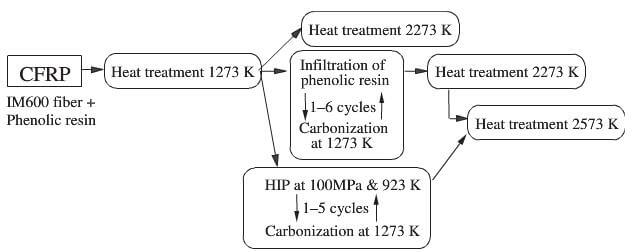
processing routes, resin char method and HIP method, of 2D C-C composites
Tensile tests:
The tensile strength and stress-strain relation of the C-Cs at various densification steps were determined using the specimens of 2mm thickness samples. The tensile tests were performed using a screw-driven mechanical testing machine, under a crosshead speed of 0.1mm/min. The tensile stress was applied to one of the fiber direction for the 2D C-Cs and fiber direction of Vf=40% for the 3D C-Cs. The tensile strain was measured using strain gages adhered to both surfaces of each specimen; the average o the measured strains was used as a representative value. To identify the fracture initiation and propagation, AE signals were monitored during all of the tensile tests.