To better understand the brake-induced sequential morphological variation under the most severe friction and wear condition, a series of SEM micrographs at different braking stages of BI/2000 were taken and compared. An example is given below.
Fig.13 showed the sequential changes in the surface morphology of BI/2000. As described earlier, the as-broken-in BI surface (Fig.13(a)) was covered with a layer of type Ⅱ powdery debris. As soon as braking started, the powdery debris started to be compacted and a smoother type Ⅲ debris started to develop (fig.(b)), causing the initially high friction coefficient to decline. With time the type Ⅲ debris continued to increase, while the powdery debris continued to decrease. After 6-8 s, the type Ⅲ debris dominated the surface, while little powdery debris was observed (fig.(c)(d)). Due to its lubricative nature of the type Ⅲ debris, the friction coefficient became minimally low at this moment. After that, the type Ⅲ debris started to lose its mechanical stability and the debris layer started to disrupt. With tim the structural damage became more severe and, at nearly the end of braking, severe damage and delamination were observed (fig.13(f)).
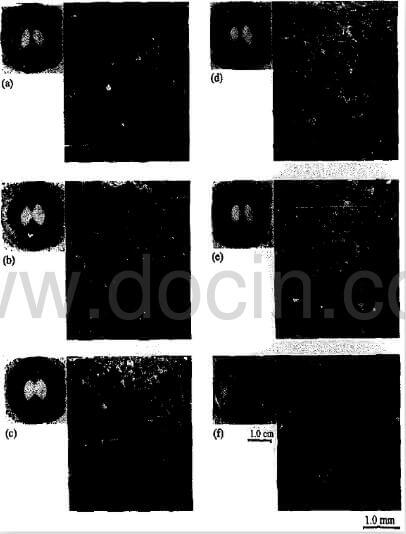
fig.13-sequential-morphological-variation-of-BI-2000
From the friction and morphological variation results, it can be seen that the friction behavior of the AP specimen (with a smooth surface and low friction coefficient), which did not undergo transition before or during braking, was relatively simple and more predictable. The friction behavior of BI specimens (with a rougher surface and higher friction coefficient), which had undergone a transition during the BI treatment, was more complex and harder to predict. ALthough such other parameters as moisture adsorption and temperature effect might play some minor roles, the friction behavior of the present C-C composite, under the present braking conditions, was most sensitive to the debris morphology. For the BI specimens, the debris morphology varies fron one braking condition to another and varies continually with braking time. This caused the friction behavior of BI/2000 to be significantly different from that of BI/1400.
The BI specimens exhibited much higher friction coefficents and wear than those of AP specimens under the same braking conditions.
Specimens braked from higher speed always suffered higher wear either due to their higher friction coefficients or longer braking times.
The friction behavior of the present composite was most sensitive to the debris morphology. The friction behavior of BI specimens, which had undergone a transition during the BI treatment, was more complex and harder to predict than that of AP specimens, which did not undergo transition before or during braking. The severe structural damage on the BI/2000 surface, which could not be mended (a stable lubricative debris layer could not be developed), resulted in an unstably high friction surface and large wear.