Structural Geometry of CC composite 2D fabrics (1)—Woven fabrics
The interlacing of yarns fabricates the hundreds of possible woven fabric combinations. From the in-plane fiber orientation, woven fabrics can be divided into biaxial and triaxial woven structures.
Biaxial weaves consist of 0° and 90° yarns interlaced in various repeating patterns or topological unit cells. The three basic weave geometrics from which many other patterns evolve are the plain, twill, and satin weaves. A schematic diagram of various views of these three basic weaves is shown in figure 6. The frequency of yarn
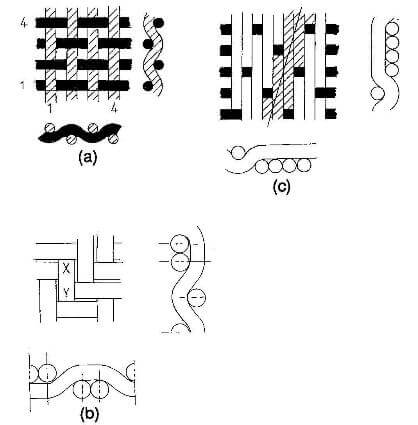
structural geometry of biaxially woven fabrics a) plain weave, b)twill weave c) satin weave.
interlacing and the linearity of the yarn segments distinguish these three fabrics. The plain weave has the highest frequency of yarn interlacing, whereas the satin weave has the least number of yarn interlacing, with the twill weave somewhere in between. Accordingly, the plain weave has a higher level of structural integrity and greater ductility because of the crimp geometry produced by yarn interlacings. On the other hand, the satin weave has the highest level of fiber-to-fabric strength and modulus translation efficiency because of the low level of yarn interlacing and yarn linearity. The low level of yarn integration in satin weave also allows freedom of yarn mobility, which contributes to higher fiber packing density and, consequently, higher level of fiber volume fraction.
Although cane weaving for cane chairs has existed for a long time, machine-made triaxially woven fabrics weren’t available until Norris Dow’s development of the triaxial weave in the early 1970’s. The unique feature of triaxial weave is the 90+/-60°hexagonal yarn orientation in on plane, resulting in a high level of in-plane shear resistance. High level of isotropy and dimensional stability can be achieved with triaxial weave at low fiber volume fraction. Figures 7 and 8 show a schematic diagram of two triaxial weave geometries.
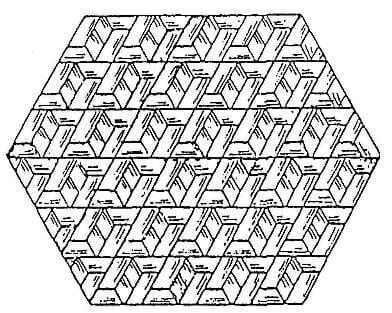
structural geometry of triaxially woven fabrics (biplain weave)
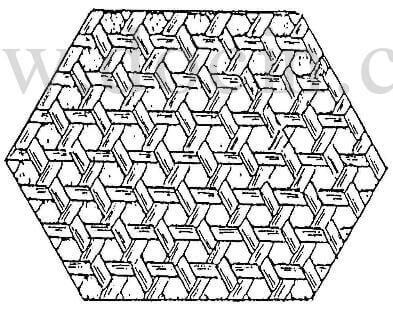
structural geometry of triaxially woven fabrics (basic weave)