The first coated CC composite was developed in the early 1970’s for use on the National Aeronautics and Space Administration (NASA) Space Shuttle orbiter vehicles. Termed reusable carbon carbon (RCC), this CC is resin-densified fabric laminate made from low-modulus, rayon-
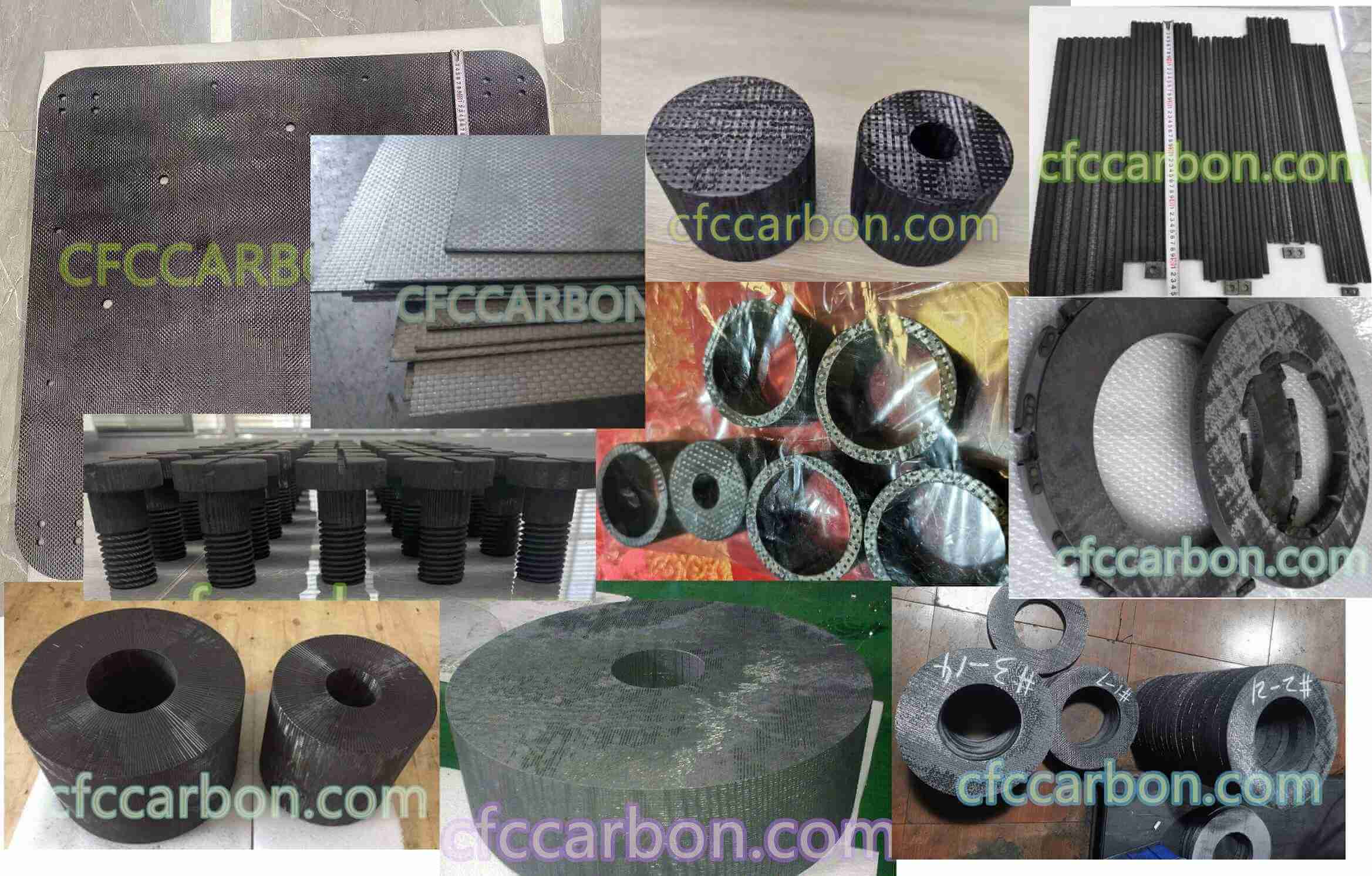
carbon fiber composite material manufacturer in China(1)
precursor carbon fibers. The RCC material is protected from oxidation by a two-layer coating system consisting of a porous SiC inner layer sealed with SiO2 and an outer coating of alkali silicate glass filled with SiC particulate. A pack process is used to convert the CC surface to SiC, followed by repeated cycles of impregnating the porous converted surface with acid-activated tetraethoxysilane (TEOS) liquid that gelled and then heated to produce SiO2. The outer coating on the carbon structure is made from a paste of commercial alkali silicate bonding liquid filled with SiC powder. The coating is applied to the structure by brushing and then it is heat-cured.
The RCC has been used to construct the nose cap and leading edge components for all of the Space Shuttle vehicles. It have performed well as a reusable thermal protection material through multiple rapid heating and cooling cycles, with short-term exposures at temperatures of more than 1300C. The durability of the RCC coating system can be attributed to several factors. First, the RCC has a
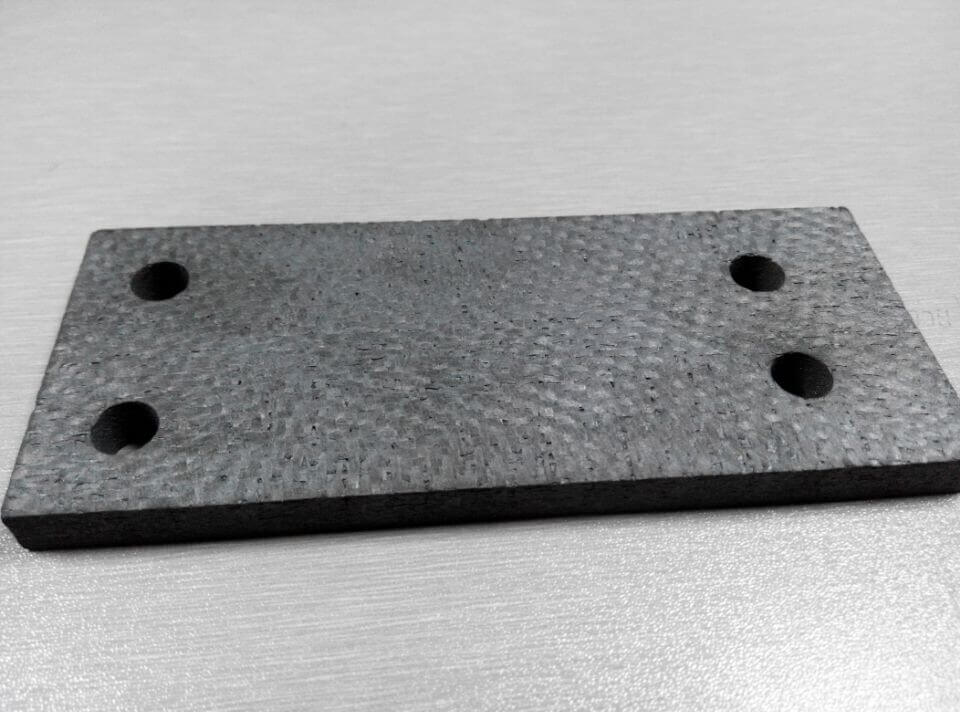
C-SIC
relatively high CTE and a low elastic modulus in the plane of the fibers. Second, the inner SiC conversion layer is a strongly bonded, integral part of the CC surface. Finally, the outer coating is a fluxed SiO2 glaze that can plastically deform at high temperatures to accommodate differential stains and is fluid enough at temperatures of more than 900C to be self-healing. A problem with the RCC outer coating is that the rate of alkali volatilization from SiO2 becomes significant in the 1200C to 1300C range, allowing the loss of the fluxing agent over periods of hours to compromise the compliancy and sealing characteristics of the glaze.
By the late 1970’s, the encouraging test results that had been obtained with the RCC material were well known. NASA’s success with CC, combined with disappointments in a Department of Defense sponsored high-performance monolithic ceramics program, generated strong DoD support for the development of oxidation-protected CC materials for very-hihg-temperature structures in advanced military systems. Although it was recognized that major differences exist between RCC and structural CC materials, it is clear that the amount of development required to meet a number of very optimistic design and performance goals has only recently been fully appreciated.
related news /articles:
Mechanical properties of CC composite –CFCCARBON LTD
Structural applications of carbon-carbon composite coatings
Coatings for carbon-carbon composites (1)-SiC oxidation
Applications of carbon-carbon composite (1)