In the early days of the carbon fiber electric lamp filament, it was the practice to coat carbonized rayon filaments with pyrolytic graphite to improve the mechanical properties of the lamp filament.
Using the chemical vapor deposition (CVD) process, a gas such as methane can be cracked onto, say a carbon substrate and when the temperature is about 1100C, it forms pyrolytic carbon, which has an isotropic nature. At 1000-1700C, the carbon deposited has a different form with an intermediate structure, whilst at 1700-2300C, pyrolytic graphite is formed. The coating can be deposited on the substrate and, if sufficiently thick, can be removed as a free-standing object (cf CVD diamond).
The structure and properties of pyrolytic deposits are influenced by a number of factors, of which temperature is the most important. The size of the crystallites and their degree of preferred orientation increases with temperature, whilst the interlayer spacing decreases. Typical values for the density, crystallite diameter and crystallite height are given in table bellow for pyrolytic carbon formd from cyclopentadiene at 930C and graphitized at 2700C. The density of 2.261g/cm3 closely approaches the value for ideal graphite (2.269g/cm3)
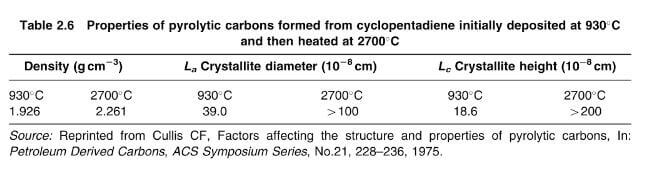
crystallite height and diameter of pyrolytic carbons
Pyrolytic graphite can be prepared through a CVD process by thermally decomposing a hydrocarbon gas such as methane, ethylene or acetylene at about 1100C by the induction heating of a substrate under taken at either a low pressure, when the product tends to be isotropic or, at pressures upto 1 atm (101kPa), when it is necessary to dilute with a non-reactive gas such as argon or hydrogen to control the deposition process.
In a simple form, the reaction can be shown as CH4-C+2H2
However, is is really more complex and proceeds via the formation of benzene, various polyaromatic hydrocarbons and is finally deposited as carbon. Other CVD deposition techniques use a fluidized bed and plasma. A variation of the CVD process used for the production of carbon-carbon employs a chemical vapor infiltration (CVI) technique, where the reactive medium diffuses into a porous substrate, such as a 3D fiber construction, but any by-products formed must be allowed to diffuse outwards, tendering the process extremely slow.
Basically, pyrolytic graphite has a turbostatic structure, which is an aggregate of graphite crystallites that can exist in certain conditions as an almost parallel array, forming a near perfect graphite crystal. By careful control, the structure of the deposit can be columnar, laminar or isotropic. The cleanliness and geometry of the substrate plays and important role in the mode of deposition. A columnar structure has the crystallites aligned with the basal planes parallel the substrate and as deposition proceeds, the columnar structures widen, becoming cone-shaped with increasing grain size, which is not a desirable factor. This cone formation can be controlled by permitting soot particles to form on the surface, providing new growth sites. A laminar structure comprises a number of parallel layers, which can be concentric if deposited on either a fiber, or a particle. Columnar and laminar structures are optically active to polarized light and can be readily graphitized at 2500C to give a high degree of crystallite alignment and if annealed further at 2700C under pressure, will produce highly oriented pyrolytic graphite (HOPG), which is an almost ideal graphite crystal.
The isotropic structure consists of fine grain with no preferred orientation and, since is has virtually no graphite structure, is termed an isotropic carbon, which does not readily graphitize and shows no optical activity.
The pyrolytic carbon is much harder, stronger, less permeable to gases and can be polished. Consequently, dimension of the resultant sheet was many times the circumference of the original whisker. The whiskers were very flexible and strong and could be bent to and from many times without breaking. Strengths as high as 20GPa were recorded with a modulus of at least 700GPa and possible as high as 1000GPa. A significant problem in testing was the ability to grip the whisker satisfactorily in the jaws of the testing machine, the low shear strength of graphite contributing to the whisker pulling out the grip and leaving an outer sheath behind. There high values have established possible targets to be achieved by carbon fibers made from polymers.