Forming techniques of graphite material: Three major techniques are used to form the graphite mix: extrusion, compression, and isostatic pressing. They are shown graphically in Fig.5.3.
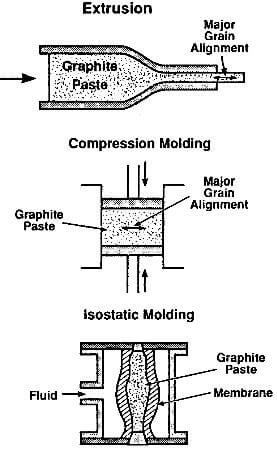
Fig.5.3-forming techniques for molded graphite
The selection of a given technique has a great influence on the final properties of the molded product as shown in table 5.2.
Extrusion: extrusion is a major technique which is favored for the production of parts having a constant cross-section, such as electrodes. The mix is cooled to just above the softening point, then extruded through steel dies, cut to length and rapidly cooled to solidify the pitch before distortion occurs. The resulting shape is known in the industry as a “green shape”.
Table 5.2. Characteristics of forming techniques
Technique | characteristics |
Extrusion | Anisotropic properotes
Non-uniformity of cross-section Presence of flow lines and laminations Limited to parts of constant cross-section Production of large parts possible Low csot |
Compression | Non uniformity
Edge effect Presence of flow lines and laminations Medium cost |
Isostatic | Isotropic properties
Uniformity No flow lines or laminations High cost |
Extrusion pressures are on the order of 7 Mpa. Some alignment of the coke-filler particles takes place which imparts anisotropy to the properties of the finished product. This anisotropy can be controlled to some extent by changing the mix formulation and the extrusion geometry. The center of the extruded material is usually of lower quality than the material near the outside edge and defects such as flow lines and laminations are difficult to avoid. On the plus side, it is the lowest-cost technique which is satisfactory for most large parts, such as furnace electrodes. It represents the largest tonnage of molded graphite.
Compression Molding. The mix in compression molding is usually a fine powder as opposed to the coarser material used in extrusion. Tungsten carbide dies are frequently used with pressures on the order of 28 to 280 Mpa. Complex shapes can be produced by this process. However, die-wall friction and die edge effect may cause non-uniformity in the density and other properties of the finished product.
Isostatic molding: In isostatic molding, pressure is applied from all directions through a rubber membrane in a liquid-filled chamber, resulting in a material with great uniformity, isotropic properties, and generally with few defects. However, the molding process is expensive and cost is higher than extrusion or compression molding.