A typical production-process flow diagram for molded graphite is shown in fig.5.2. The production steps are as follows.
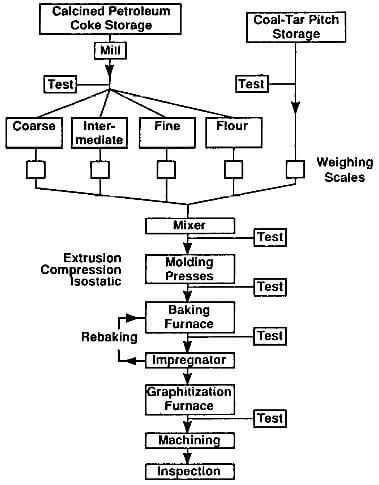
fig.5.2-producton process flow diagram of molded graphite
Milling and sizing: filler and binder are ground or milled to the particle-size requirement which may vary from 1 um to 1.25 cm. A batch usually consists of more than one size. This allows better control of the packing characteristics and optimizes the density of the final product. Table 5.1 lists the grain size of various grades of molded graphites and its effect on properties.
Table 5.1. Particle sizes and characteristics of graphite grades
Grade | Grain size | properties |
Medium grain | Up to 1.25 cm | Low density |
Low thermal expansion | ||
Low strength | ||
High permeability | ||
Fine grain | 0.05 to 0.15 cm | Medium density |
Medium thermal expansion | ||
Medium strength | ||
Medium permeability | ||
Micrograin | <1 um to 75 um | High density |
High thermal expansion | ||
High strength | ||
Low permeability |
Mixing: filler and binder are weighed in the proper proportion and blended with large mixers into a homogeneous mix where each filler particle is coated with the binder. Blending is usually carried out at 160-170C, although temperatures may reach as high as 315C on occasion. When mixing at lower temperatures, volatile solvents such as acetone or alcohol are often added to promote binder dispersion.
The final properties of the molded product are controlled to a great degree of the characteristics of the filler-binder paste such as: (a) the temperature dependence of the viscosity, (b) the general rheological behavior, and (c) the hydrodynamic interaction between filler particles.