Structural Geometry of CC composite 2D fabrics (2)—Knitted fabrics and Braided fabrics
Knitted fabrics are interlooped structures wherein the knitting loops are either produced by the introduction of the knitting yarn in the cross-machine direction or along the machine direction. As shown in figure 9 and 10, knitting can produce a large number of stitch geometries. By controlling the stitch density, a wide range of pore geometry can be generated. Because of the nature of the interlooped structure, the maximum fiber packing density of knitted structures is lower than that of the woven fabrics. The severe bending of yarns during the knitting process also
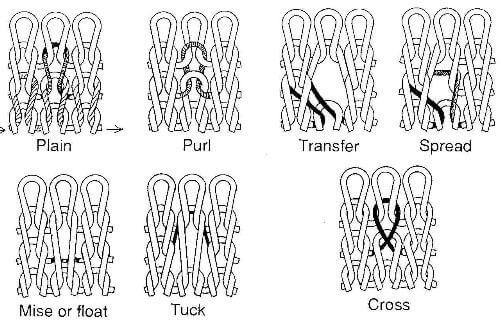
weft-knit constructions
discourage converting ceramic yarns to knitted structures. However, if a creative combination of ceramic sewing threads or very fine yarns is used to form the stitches, knitted fabrics may be used effectively as a base structure for the incorporation of 0° and/or 90° yarns. The resulting preform is an integrated structure that combines the high conformability of the knitted base structure with a high level of directional reinforcement from the straight lay-in yarns.
Braided Fabrics
By intertwining three of more yarn system together, braided fabrics can be produced in flat or tubular form. The bias interlacing nature of the braided fabrics make them highly conformable, shear resistant, and tolerant to impact damage. To enhance reinforcement in the
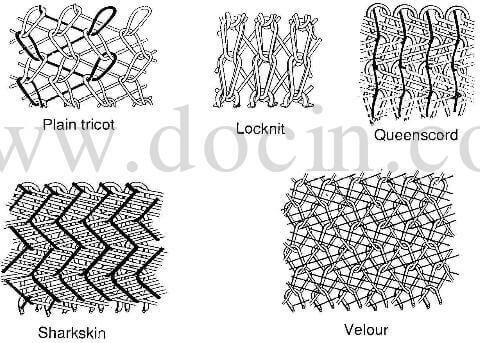
warp-knit constructions
0°direction, triaxial braiding can be used to introduce 0+/- x yarns as shown in figure 13. Although braiding and filament winding bear some similarities, subtle differences exist between these two processes and resulting structures. Table3 provides a comparison of braiding and filament winding. In other articles, we will talk about the braiding in details.