Cracking between subregions within the unit cell occurs as a result of cooldown from the graphitization cycle during fabrication of CC composites. The fibers in current CC composite materials have a much lower axial thermal expansion coefficient than the matrix material.
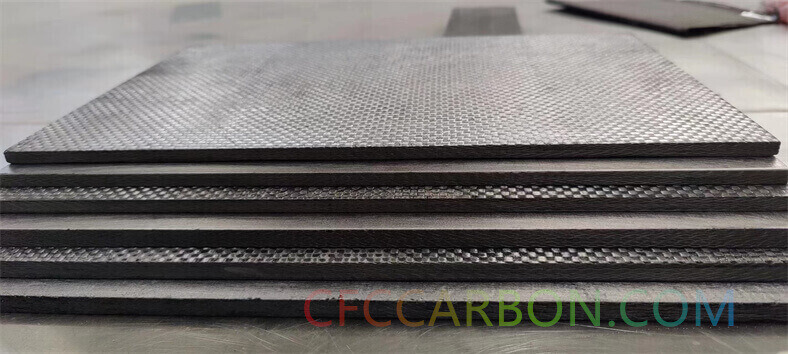
carbon fiber composite plates sheets U L profiles-2D material manufactuer china (5)
Because the material is graphitized at high temperature, the material becomes stress free at that temperature. Upon cooldown, the matrix is loaded in tension since it tries to contract at a much higher rate than do the fibers. This loading results in cracks occurring between the fiber bundles and the matrix material. The degraded properties model was developed specifically to include the effects of cooldown cracking upon resulting composite properties. Actual crack geometry and crack-tip stress intensity effects have not been considered. Rather, the model considers the ability of the material to transmit loads across the interface between subregions within the unit cell.
The weak regions are approximated as thin plate-like regions in which the thickness of such regions is assumed to be small in comparison to the dimensions of the subregions and the unit cell. In order to develop a simple
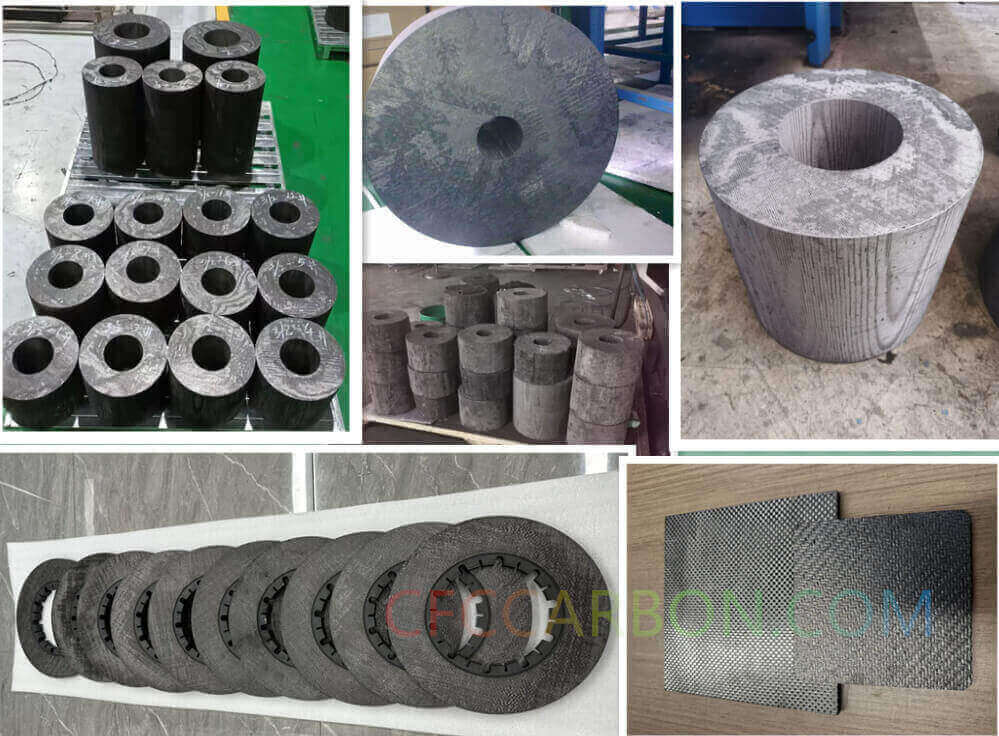
2D 3D 4D 5D carbon fiber composite material manufacturer factory -airplane brake disc plates sheets U L profiles-2D(6)
analytical model that yields a suitable representative volume element, all parallel planes of weakness are assumed to have similar stress transfer characteristics, although each of the unit cell interconnecting surfaces may have its own unique stress transfer characteristics defined, if desired.
The inclusion of regions of degraded load transfer capability in DCAP requires some definition of the effectiveness of the degraded material layers in transmitting axial and shear loads between subregions. The efficiency of the degraded material may be considered equivalently as the stress transfer capability or as a measure of the stiffness of the degraded material.
Both the degraded property model and the basic multidirectional composite model treat thermomechanical properties including the effects of temperature-dependent constituent properties. Thermal expansion data are defined for the constituents in the form of free thermal expansion versus temperature. The model then can compute secant thermal expansion coefficients for each subcell of the unit cell from the analysis temperature to the reference stress-free temperature. The secant thermal expansion coefficients for the subcells are then combined to form the composite thermal expansion coefficients. The resulting values for the composite, from the stress-free temperature to the given temperature, are used to obtain a set of predicted composite thermal expansion coefficients versus temperature.
The output of the model provides all the thermoelastic properties of te unit cells for each desired temperature. In addition, if composite stresses are applied, the unit cell strains and average strains and stresses in each subregion can be computed for each temperature. An example of properties prediction and correlations with experimental data follows.
related news /articles:
Description of CC composite model
Structure and properties of textile-reinforced carbon-carbon composite
Friction performance of C/SiC brakes in different environment (10)
Concluding remarks for CC composite models