To obtain dense reaction products in the interlayer, an axial pressure is necessary for the joining couples. The effect of the joining pressure on the joint microstructure is shown in Fig.5. When a lower pressure (20Mpa) is applied, large pores are produced in the products. When the joining pressure is increased to 40Mpa, dense reaction products are obtained and no obvious pores are observed. The higher pressure is beneficial for the densification of the reaction products. Therefore, the pressure of 40Mpa was applied in other experiments in this study. However, too high pressure should not be applied due to the weakness of the C/C substrates. White et al. also suggested that the application of high compressive loads of 51Mpa followed by rapid unloading led to C/C composite exfoliation.
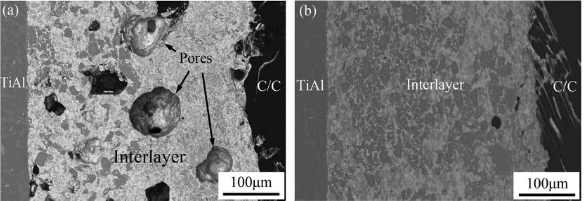
Fig.5-effect of the joining pressure on the microstructure of the TiAl-CC joint (a) 20Mpa, (b) 40Mpa.
The TiAl-C/C joint microstructure is presented in Fig. 6. The overall view in Fig. 6 (a) indicates that the interfaces appear to be well-bonded. The interfacial area can be divided into three zones: Zone 1, Zone 2 and Zone 3. No defects are observed in the joint, and the interfacial reaction is sufficient. We note that the added Ag-Cu-Ti filler metal is difficult to be distinguished, which indicates a sufficient melting and reaction of the filler metal. The microstructure between the composited interlayer and the C/C substrate is shown in Fig.6(b). The corresponding EDS analysis results are listed in Table1. A thin reaction layer is observed adjacent to the C/C substrate, which is identified as the TiC layer. Because the formation of TiC is thermodynamically favorable, the TiC layer usually formed at the interface between the C/C substrate and the Ti-containing filler metal, as demonstrated in Refs.
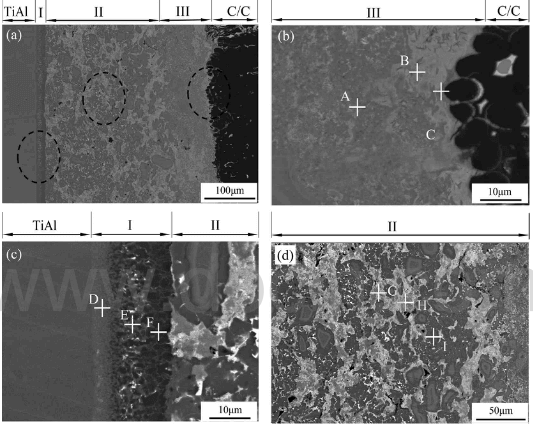
Fig.6-microstructure-of-the-TiAl-CC-joint-aoverall-view-b-on-the-CC-side-c-on-the-TiAl-side-d-in-the-interlayer
Fig. 6(c) presents the interfacial microstructure on the TiAl substrate side. There are complex reaction layers observed in this zone. The exothermic reaction in the interlayer leads to a drastic increase in the interfacial temperature and results in a special microstructure near the TiAl substrate. The reaction layer at Point D mainly
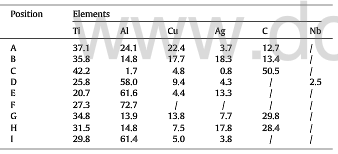
EDS results of the TiAl-CC joint in fig.6 (at %)
consisted of Ti-Al-Cu intermetallic, which was similar with the results using a Ag-Cu-based filler metal. We note that the white phase at Point E was preferentially enriched with Ag, which was important for the local melting of the zone adjacent to the TiAl substrate. The reaction layer at Point F was only composed of Ti and Al elements. The concentration of the elements indicates the formation of TiAl3 in the layer. Fig. 6(d) displays the microstructure of the reaction products in the interlayer. The reaction products primarily consisted of TiAl3 and TiC phases, which was in agreement with the XRD results in Fig.2. Additionally, small amounts of Ag-based solid solution were detected in the light phase marked by Point H.
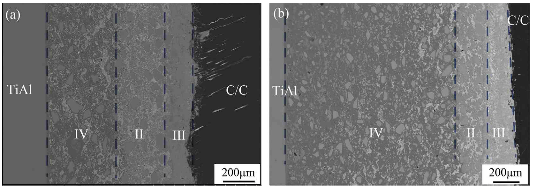
Fig.7-effect of the interlayer thickness on the TiAl-CC joint microstructure (a) 1mm (b)2mm
The total heat generated by the reaction is proportional to the thickness of the interlayer. The effect of the interlayer thickness on the microstructure is shown in Fig. 7. The TiAl-C/C joint devoid of interfacial defects is formed using two interlayers with different thickness. The number of reaction layers is the same for these two interlayers. However, the fraction of layer 2 and 3 using a 2mm interlayer is relatively low compared with the 1mm interlayer due to the limitation of the filler metal. The thick interlayer is easier to condense than the thin interlayer, as shown in Fig. 6. Similar results were also reported by White et al, and they concluded that there is a critical thickness of 500 um for condensation.
The adiabatic temperature is determined by the composition of the interlayer, which also affects the joint microstructure greatly. The microstructure using different interlayers is shown in Fig. 8. When the interlayer with low adiabatic temperature was added, the reaction heat was insufficient for the densification of the reaction products, resulting in pores in the reaction products. For the interlayer with a high adiabatic temperature, the reaction both at the interface and in the interlayer is sufficient. Dense reaction products and a defect free joint were achieved.
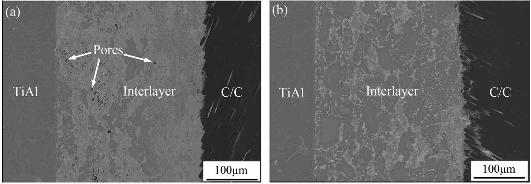
Fig.8-effect of the interlayer compostion on the TiAl-CC joint microstructure (a)m=0.4 (b) m=1.1
In this study the pores were almost eliminated because of the optimization of the processing parameters and adding of the Ag-Cu-Ti filler metal. However, for most SHS process using the powder interlayer a high porosity remained a general problem. For the processing parameters, the joining pressure played an important role on the porosity of the reaction products. The porosity decreased significantly when a higher pressure was applied. However, too high of a pressure will deteriorate the properties of the substrate and the self-sustaining reaction of the interlayer. Another possible approach is to introduce the Ag-Cu-Ti filler metal into the reaction system. After the self-sustaining exothermic reaction was ignited, the filler metal was melted by the reaction heat. The melting filler metal fulfilled the residual pores in the products via wetting. Therefore, to decrease the porosity of the SHS reaction products, a moderate pressure and a sufficiently active liquid phase, which could wet the products and fill the possible pores, were needed for the densification of the products.