The relationship between the interlayer composition and shear strength of the joint is shown in Fig. 9 (a). When an interlayer with a low m value corresponding to low exothermic heat was used, the shear strength was low due to an insufficient interfacial reaction. With an increase in the m value, the exothermic heat of the self-sustaining reaction increased, and the interfacial reaction became sufficient. In addition, the densification of the products in the interlayer was complete, as shown in Fig.8. These factors led to the increase in the shear strength of the point, and the highest value for the shear strength, 17.6Mpa, was obtained when the m value was 1.1. When the exothermic heat further increased with an increasing m value, the joint strength started to decrease, which may be due to the thick interfacial reaction layer. In addition, the joint strength was much higher when a high joining pressure was used than when a low pressure was used, which was in accordance with the microstructural analysis results.
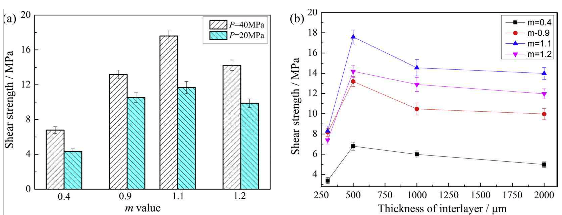
Fig.9-effect of interlayer composition and thickness on the shear strength of the joint (a) interlayer composition ( b) interlayer thickness
The dependence of the shear strength on the interlayer thickness is shown in Fig.9(b). When the interlayer thickness is small, the shear strength is low due to an insufficient interfacial reaction. The heat generated in the interlayer was transferred to the substrate to heat the interface. An interlayer with small thickness cannot generate enough heat for a sufficient interfacial reaction. With the increase of the interlayer thickness, the total exothermic heat increased, and the reaction became sufficient. The molten filler metal can fill the voids of the reaction products, and a defect-free joint was obtained. The shear strength reached a maximum value of 17.6Mpa when the thickness of the interlayer was 500 um. When the thickness increased further, the molten filler metal was insufficient, and the reaction products with pores lead to a decrease in the joint strength. In general, the joint strength depended upon the interfacial joining and the overall properties of the reaction products. An increase in the interlayer thickness causes an increase in total exothermic heat, which is beneficial for improving the interfacial joining quality. However, the molten filler metal cannot fill the pores of the reaction products in the thick interlayer in which the joint with defects was manufactured, and the joint shear strength correspondingly decreases. The heat generated by the reaction is determined by the composition of the interlayer. It was noted that the strength was sensitive to the adiabatic temperature change. When the adiabatic temperature was 2636.7K, the highest shear strength was obtained. However, if the adiabatic temperature was changed to 2677.3K, or 2546.5K, the shear strength of the joint decreased greatly even though the temperature change was less than 100K. Therefore, although this approach is a local heating and energy-efficient process, the processing temperature window is relatively narrow compared to the other joining methods such as brazing or diffusion bonding.
The fracture surface was analyzed, and the results are given in Fig.10. There are two types of fracture after the shear test of the TiAl-CC joint. For the joint with the highest shear strength, the fracture mainly propagated in the C/C substrate, and carbon fibers were observed on the fracture surface, as shown in Fig. 10(a). For the joint with low strength, the fracture mainly took place at the interface between the interlayer and the substrates. In addition, most of fracture propagated across the interlayer from one side to the other side, which indicated the low quality of the interlayer. Because the strength data of the C/C substrate used in the literature is different, it is not appropriate to simply compare the strength values. The failure along the C/C substrate indicates that the joined layer is mechanically stronger than the C/C substrate.
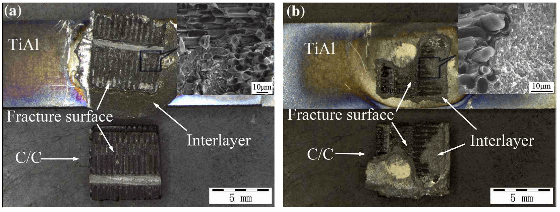
Fig.10-the fracture of the TiAl-CC joint using Ti-Al-C interlayer (a)along the CC substrate, (b) across the interlayer.
The interlayer for combustion joining can be divided into two series. The first series of interlayer primarily consists of an active metal and a nonmetal with a small atomic diameter, such as C or B. The adiabatic temperature is high, and a self-sustaining reaction tends to proceed. White et al. used this series of an interlayer containing Ti+C and Ti+B +C to successfully join C/C composites. However, the tensile strength of the joint was no more than 8Mpa, which is due to the low quality of the reaction products in the interlayer. The other interlayer series was composed of an active metal mixture, such as Ti+Al+Ni or Al+Ni. Duarte and Simoes etal performed the combustion joining of TiAl using Ti/Al or Al/Ni mutilayer foils. The metallic system is easy to ignite, and the reaction products present better plastic properties, which is beneficial for releasing the residual stresses. Lin et al. carried out the combustion joining of C/C using a reactive mixture of Ti and mechanically activated Ni/Al powders. However, the CTE of the reaction products of the metallic interlayer was much larger than that of the C/C substrate, leading to the generation of residual stresses during the cooling stage. These residual stresses derived from the CTE mismatch negatively affected the joint properties and even resulted in a crack at the interface, as demonstrated in our previous work.
The experiments in this study were carried out to improve the wettability of the C/C composites and to reduce the CTE mismatch. First, an AgCuTi active filler metal was added in the composite interlayer to improve wetting of the C/C composites. Many studies have demonstrated that the Ti-containing filler metal can wet the C/C composites very well by forming Ti-C compounds. Second, the Ti-Al interlayer was selected to gradually transition the CTE from the TiAl to the C/C composites, the CTE of the TiAl and the C/C composites are approximately 14.4 ×10-6 and 4.0×10-6, respectively. The predominant product of the interlayer is a mixture of TiAl3 and TiC. Therefore, the CTE of the interlayer products is between that of the TiAl and C/C composite substrates. Based on this, a distribution of the thermal stresses generated by the CTE mismatch can be improved.
In this study, the Ti-C reaction ensured a sufficient reaction heat to produce interfacial joining. The addition of Al decreased the ignition temperature, and the self-sustaining reaction was ignited at a low temperature. To improve the joint quality, the Ag-Cu-Ti filler metal was added between the interlayer and the C/C substrate. The molten filler metal filled the reaction product pores and produced interfacial joining of the C/C substrate. Although the melting point of the Ag-Cu-Ti filler metal was low, the joint still had a better high temperature performance because the main structure of the joint was a mixture of TiAl3 and TiC in which the composite structural products were formed.
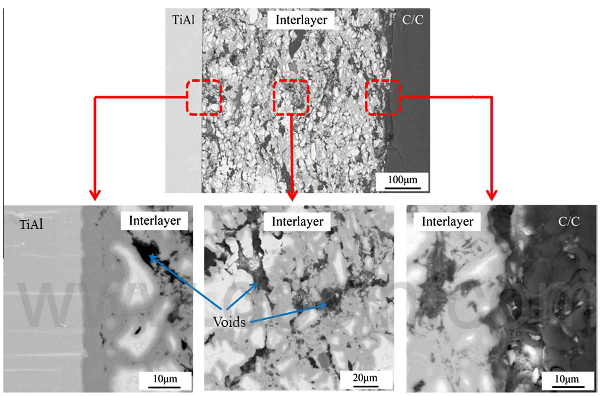
Fig.11-the TiAl-CC joint microstructure without the Ag-Cu-Ti filler metal
To evaluate the effect of adding the Ag-Cu-Ti filler metal on the composite structure, the joint microstructure only using the Ti-Al-C interlayr is analyzed in Fig.11. We observed that the joint was composed of large amounts of voids and only a portion of the interface was joined between the interlayer and the C/C composites, whereas the interfacial joining on the TiAl side was acceptable. The unsatisfactory microstructure was formed from the lack of wetting and filling by the Ag-Cu-Ti filler metal. The highest shear strength of this joint was only3.1 ±0.8Mpa, which is much lower than when the Ag-Cu-Ti filler metal was added. Therefore, compared to the joint without adding the Ag-Cu-Ti filler metal, this Ag and TiAl3 composite structure improved the joint quality.