In addition to the seal applications mentioned above, molded graphite has many applications in areas where chemical resistance is the major factor. Such applications are found in chemical reactors, heat exchangers, steam jets, chemical-vapor deposition equipment, and cathodic-protection anodes for pipelines, oil rigs, DC-power lines, and highway and building construction.
Nuclear applications: Molded graphite is one of the best material for nuclear-fission applications since it combines high neutron-moderating efficiency and a low neutron-absorption cross section, good mechanical strength and chemical resistance, ease of machinability, and relatively low cost.
However, nuclear radiation affects the crystal lattice which becomes distorted by collisions with fast neutrons, other energetic particles, and displaced carbon atoms. As a result, the properties are altered to some extent. Strength and hardness generally increase and dimensional changes become noticeable particularly at high temperature, as shown in Fig.5.17.
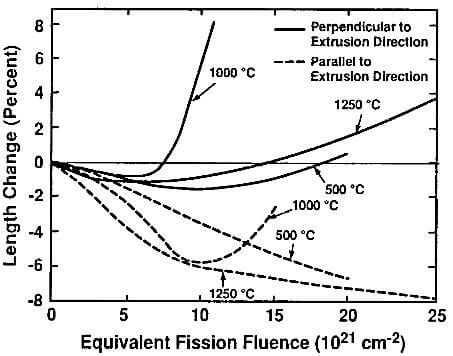
fig.5.17-length changes of typical nuclear graphite as a function of fission fluence
Nuclear graphite is usually manufactured from high-grade coke filler and pitch binder, processed as described earlier in this chapter, and then thoroughly purified by halogen treatment. The highest degree of purity is necessary to attain the required nuclear properties.
The material was the building block of CP-1, the world first nuclear reactor at the University of Chicago, and will form the nuclear core for the new generation of high-temperature gas-cooled reactor. Tentatively scheduled for construction in the mid-90’s. It is presently used as fuel-element blocks, replaceable or permanent reflectors, and other components.
Molded graphite is also used in experimental fusion reactors such as the Tokomak Fusion test reactor as interior liners, movable limiters, and specialized fixtures, where its low atomic number is an important factor in reducing interference with the fusion reaction.