SEP first investigated carbon-carbon as a candidate for brakes in 1972 and became involved with aircraft brake from 1978, whilst Carbone Industrie became involved from 1986. SEP was able to draw heavily on its own experience gained developing carbon-carbon for rocket propulsion, having produced commercial quantities of carbon-carbon from 1974 onwards. Carbon-carbon brakes were tested by Carbone Industrie on Formula One racing cars in 1997, enabling and F1 racing car to decelerate without fading from 350 to 100 km/h in three seconds, the mechanical characteristics improving as the temperature rose and lasting up to some six times longer than a conventional braking system. The braking performance of carbon-carbon at high speeds is exceptionally good and Cl has developed brakes for France’s TGV trains, which operate in commercial service at speeds up to 350km/h. It is likely, however, that carbon /SiC brake disks may offer improved performance in this application.
The friction, or efficiency factor(μ), of a brake varies during the braking process and initially, with a carbon-carbon brake, μ increases as the operating temperature rises, with fading occurring only at extreme temperatures, when other materials would have long since failed. For instance, each brake in an Airbus jetliner absorbs 70 MJ of energy, stopping the aircraft in 1,300m with the peak temperature of the carbon-carbon rising to 2,300C. Typical energies absorbed by each brake for various transport systems are given in Table 23.15.
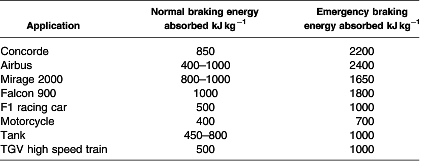
table.23.15-energy absorbed per brake in various systems of transport
In 1975, General Dynamics awarded Goodyear Aerospace Corporation the carbon brake contract for the F-16 fighter jet aircraft and the carbon-carbon was supplied by H company. Goodyear discontinued support for F1 racing cars in 1986 and the following year, Goodyear aerospace became Loral Defense Systems.
H company, following the successful development of carbon-carbon brakes for military and commercial aircraft, investigated carbon-carbon as brake materials in high performance racing cars. This development is recorded by Gibson and Taccini. The brakes comprised one disk and two pads. Team Brabham became interested in carbon-carbon brakes in the late 1970s and in 1980, obtained encouraging results in the Long Beach F1 Grand Prix race and entered into an agreement with H company to develop a carbon brake for F1 racing circuits. Initial trials were retrofits of the cast iron brake rotors, which would always be a compromise. Racing car brakes are used repetitively and an major initial problem was the boiling of the brake fluid due to the heat dissipated by the high surface temperature of the carbon-carbon. This was subsequently accommodate by increasing the air flow to the rotor facings and heat conduction from the pads by positioning an asbestos/phenolic insert between the caliper piston and brake pads. Investigations revealed a critical temperature of about 700C, which exceeded, would dramatically increase pad wear due to increased surface oxidation. At 120C, wear rates for rotor and pad were 0.06 and 0.09mm per 100km, but if the temperature rose to 220C, were became 1.89 and 1.26mm per 100km. Hence, the brakes were quite satisfactory on a light/medium braking circuit, but were not adequate on heavy to severe braking circuits, where the wear rate on front wheel pads increased by a factor of 3.Driver’s experience found that the carbon-carbon brakes required less effort, had no fade, required less distance for deceleration and showed an improvement in acceleration after severe braking due to a significant weight advantage. An agreement in 1984 with Automotive Products plc saw further improvements to the brakes, such as using a larger diameter rotor and increased disk thickness, which resulted in less were due to the higher mass heat sink effect which resulted in lowered surface temperature, combined with improved radial cooling within the disk.