Several C/SiC components like flame-holders, exhaust cones and engine flaps have proven their feasibility for military jet engines. Outer flaps in the S-M88-2 engine provide 50% weight savings over the corresponding superalloy flap and almost 300 flaps have been
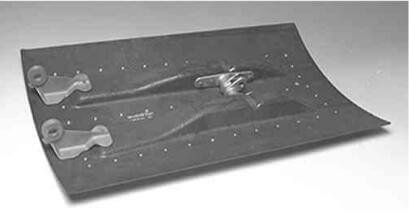
Fig.4-C-SiC outer flaps of the M88-2 engine
fabricated for ground tests (fig.4). C/SiC engine flaps are of price interest for future military engines where they allow the reduction of internal cooling flow, thus yielding benefits in the engine performance.
The general low resistance to oxidation of carbon only permits restricted operational periods of the C/SiC structures at temperatures above about 450°C. Its utilization in civil aircraft turbines or stationary gas turbines (e.g. as tiles in conbustion chambers, for diffusers or for turbine vanes) with operational times of several 10,000 hours is therefore not possible from today’s point of view even with very sophisticated multi-layer protiective coatings. The current terrestrial C/SiC developments are therefore concentrating on applicatons that have a performance range demanding a resistance to high temperature only for a short time, or on products, which make use of other advantageous characteristics of these multiphase composites.
Advanced friction systems:
C/C-SiC composites, made by liquid silicon infiltration (LSI-process), offer superior tribological properties in terms of high coefficient of friction (CoF) and wear resistance. The carbon fibers lead to an improved damage tolerance in comparison to monolithic SiC, whereas the silicon carbide matrix improves the wear resistance compared to carbon/carbon. C/C-SiC composites are therefore new, outstanding materials for brakes and clutches of high speed cars, trains and emergency brakes in the field of mechanical engineering and conveying.
First attempts to investigate C/C-SiC composites for their use as frictional materials for brake pads and disks started in the early nineties. C/C-SiC materials show, in comparison to carbon/carbon, a considerably lower open porosity (less than 5%), a moderately higher density (about 2g/cm3) and a ceramic share of at least 20% in mass. Several activities in institutes as well as in industries now exist to investigate CMC materials for their use as frictional materials for brake pads and disks. The resulting materials differ in their constituents, microstructur, properties and also in their processing conditions. Nevertheless, they are all based on carbon fibers and silicon carbide matrices as the main constituents of the composite material. The carbon fibres generally decrease the brittleness of SiC considerably so that the damage tolerance of C/C-SiC components lies in the same order of magnitude as for grey cast iron.
For automotive use, especially for high performance disks the costs of continuous fibres and the common processing techniques for
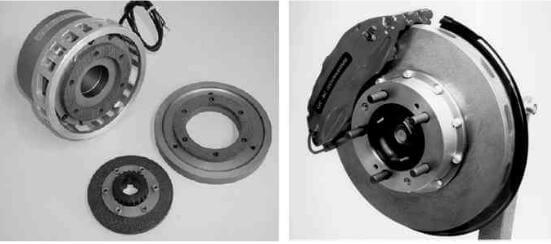
Fig.5-emergency brake system and internally ventilated brake disk for passenger cars, made of CC-SiC
components used in aerospace are too high for a srial production with high numbers of items. The most promising way to reduce the costs and to simplify the manufacture is to employ short fibre reinforcements and pressing technique. The use of short fibers reduces the costs of the raw materials primarily by the reduction of waste in comparison to bi-directionally woven fabrics. Due to the more isotropic fibre orientation of short fibre reinforced C/C-SiC the thermal conductivity perpendicular to the friction surface of brake disks is generally higher compared to the orthotropic material based on laminated woven fabrics. This leads to lower surface temperatures on the brake disks resulting in an higher and more constant coefficient of friction and lower wear rates. In different tribological test campaigns the performance and the excellent wear resistance were proven and new constructions suitable for these new braking materials were developed (Fig.5). Due to their high thermal stability and their low weight a great leap in brake technology is achievable, combining non-fading characteristics with better diving dynamics. Different passenger cars are already equipped with ceramic brakes and clutches in series and several industrial companies are currently producing or developing C/C-SiC frictional parts in an advanced stage.
Emergency stop brakes of different constructions are used in many fields of engineering, for example in lifts, cranes, electric drives for machine tools and winds. Electromagnetic spring applied brakes are commonly used for braking or holding loads, which are closed in the de-energized condition. The brake system often consists of a rotating and two stationary brake disks similar to heat pack of aircraft brakes. Increasing drive and higher circumferential velocities in modern power transimission necessitate new concepts.
New C/C-SiC composites have been developed and investigated in order to increase the efficiency of emergency brakes. Tribological tests have shown low wear rates and high coefficients of friction even at high energy input, whereas conventional friction material are completely overloaded. The benefits for the customer comprise a higher transmitted braking power and smaller dimensions of the brake systems, equipped with C/C-SiC pads. Presently, different carbon fibre reinforced ceramics are developed and commercially available to be used in high performance brake systems.
To continue…
Related news /knowledge:
- Carbon fiber reinforced silicon carbide composites (C/SiC, C/C-SiC)-(2)-application
- Carbon fiber reinforced silicon carbide composites (C/SiC, C/C-SiC)-(4)-application
- Carbon fiber reinforced silicon carbide composites (C/SiC, C/C-SiC)-(6)-processing
- Carbon fiber reinforced silicon carbide composites (C/SiC, C/C-SiC)-(7)-processing