C/SiC and C/C-SiC applications lie in fields where conventional materials, due to their insufficient mechanical properties at high temperatures or limited damage tolerance behaviour can no longer be considered and includes in principal all areas of lightweight construction. Some examples are given for high temperature (T>1000°C), medium temperature and low temperature (T<450°C) regimes.
Space vehicle’s TPS and Hot structures:
Temperaures of up to 1800°C occur during the re-entry phase of orbiters into earth’s atmosphere. Thermal protection systems (TPS) are the domain of carbon fiber reinforced SiC-ceramics in spacecraft structures and numerous technology-driven projects have been performed over more than two decades in Europe, the US and Japan. The Hot structures of NASA’s experimental space vehicle X-38, which was planed to serve as a technology carrier for a new Crew Return Vehicle of the international space station, are regarded as an example for the current stage of C/SiC and C/C-SiC development for thermal protection systems. A nose cap, the adjacent thermal protection panels, two leading edge segments and two body flaps for the steering of the vehicle were manufactured and qualified by ground-tests by a German consortium.
The nose cap made of LSI-C/C-SiC by DLR is particularly exposed to extreme temperature stresses upon re-entry due to its location
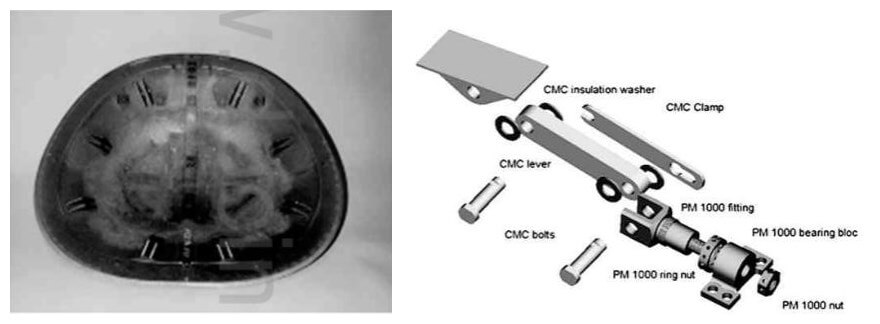
Fig.1-attachment design of the X-38 nosecap, made of CC-SiC composites
directly in the stagnation region of the vehicle. The connection of the nose shell to the fuselage consists of eight individual mounting braces, which are also made of C/C-SiC, or respectively in the cooler areas, of a temperature resistant metal alloy. This lever-type fastening system guarantees high durability against mechanical stress, and it also allows an unhindered thermal expansion of the shell, which may amount to s much as three millimeters at a mean diameter of 700 mm at the expected temperature level of 1750°C (Figure 1)
The CVI-C/SiC body flaps, are build up from four boxes with integral transverse stiffeners and flanges to bear covers. The flaps of
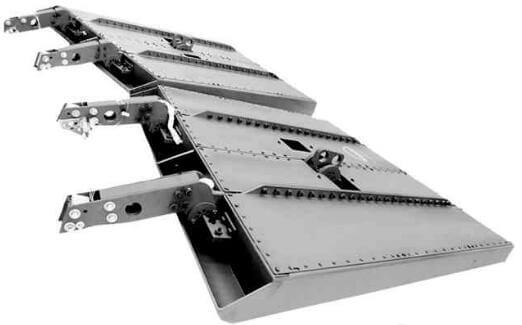
fig.2-CVI-CSiC body flaps for the X-38, joined with CSiC screws.
1600mm in length and 1500mm in breadth are joined with more than 40 screws in tot, also made of CVI-C/SiC (fig.2). The use of C/SiC composites is providing about 50% weight reduction with higher safety margins compared to insulated metallic structures. The C/SiC nose skirt was manufactured via the liquid polymer infiltration process.
Vanes, nozzles and flaps of rocket motors and jet engines:
Even shorter operational times than those occurring during re-entry are demanded of jet vanes which are used to divert the direction of thrust in solid fuel rockets, but they are loaded by considerably higher stresses, Fig.3. The controllable vanes provide an increased manoeuvrability of the rockets, primarily during the low-speed phase immediately after take-off. Only a few seconds of evendurance are required, but these few seconds impose upon the material the utmost demands regarding thermomechanical stability and resistance to abrasion. The C/SiC vane surfaces
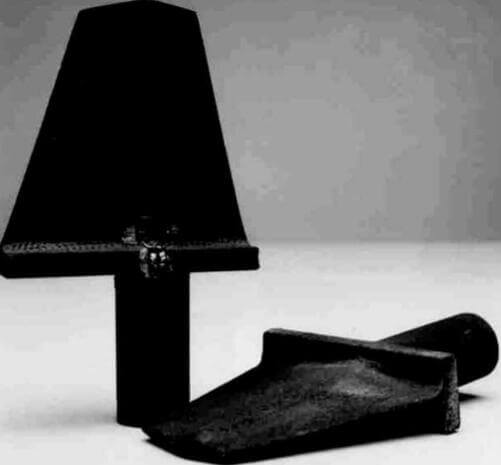
Fig.3-CC-SiC jet vanes for solid fuel rocket propulsion systems
should be additionally coated with a protective ceramic coating in order to be able to withstand the immense blast of particles occuring as the solid fuel burns away. At the same time, the ceramic content of the stucture material must be at such a high level, that the unavoidable burn-up consumption takes place only gradually, so that a sufficient residual vane surface is available during the complete buring period. The formulaton of the microstructure of the C/SiC composite consequently requires an optimization of the conflicting demands for high fracture toughness and high resistance to abrsion.
C/SiC composites have also been investigated successfully for expansion nozzles of rocket propulsion systems. Exemparily, a nozzle demonstrator of the upper stage engine of Ariane 5 was designed and manufactured by filament winding, using LPI techinque. The nozzle with a length of 1360mm and an exit diameter of 1330mm showed a mass of 16kg. Although considerable thicker wall structures were necessary, weight reductions of 60% and an increase of the allowable temperature of about 500°C in comparison to suprablloy Haynes 25 cound be achieved.
to continue–
Related news /knowledge:
- Carbon fiber reinforced silicon carbide composites (C/SiC, C/C-SiC)-(1)
- Carbon fiber reinforced silicon carbide composites (C/SiC, C/C-SiC)-(3)-application
- Carbon fiber reinforced silicon carbide composites (C/SiC, C/C-SiC)-(6)-processing
- Carbon fiber reinforced silicon carbide composites (C/SiC, C/C-SiC)-(7)-processing