Currently about 81% of carbon-carbon composite materials (CCCM) are used in aircraft brake disks, about 18% are used in space rocket technology, and only 1% are used in the rest of the spheres of applications. In recent years the production of brake disks throughout the world has grown steadily, by about 12% each year.
Development of the technology for preparing carbon-carbon brake disks for aircraft, automobiles, and other applications using thermal-gradient gas phase methods, and also a method for a radially moving pyrolsis zone is particularly important today for the Ukraine in view of the creation in “Antonov” ANTK of new domestic aircraft and preparation of them for production.
Today practically all of the brake disk output in the USA, France, and other countries is produced using liquid- or gas-phase isothermal methods for densification with pyrocarbon. These methods have many disadvantages such as the considerable duration and multistage nature of the process, and the requirement to remove the surface skin in order to reveal the transport pores, which leads to a loss of expensive material.
In developing the technology for preparing brake disk billets we have used thermal-gradient gas-phase methods for densifying porous materials developed in the National Scientific Center, in particular a method for a radially moving pyrolysis zone. As for vapor-phase methods, these are free of the disadvantages inherent in liquid- and gas-phase isothermal methods and they are acknowledged as the most promising for brake disks.
Brake disks are one of the few fields of applications of CCCM where high quality materials are required, primarily of high density. This is due to the fact that at the instant of braking kinetic energy is converted into thermal energy and it accumulates in the brake disks. Today throughout the whole world a requirement for density of not less than 1.7 g/cm3 is imposed on materials for brake disks (many for aircraft). Another important factor in choosing CCCM for producing brake disks is their mechanical strength. However, in our view this requirement results from shortcomings for the brake disk fastening assemblies and it does not play a marked role.
Thus, we encounter a problem: on one hand, a considerable content of carbon fiber is required in the material, which provides its high mechanical strength, and on the other hand, the high carbon fiber content with low density reduces the final density of the brake disks.
Choice of the optimum specific carbon fiber content by experimental methods alone is difficult, which is connected with the considerable duration of production technology, difficulties in providing with identical conditions, the comparatively high cost. In order to solve this problem we suggested an equation making it possible to calculate the maximum final density of the material obtained by thermal-gradient gas-phase methods in relation to the specific content and density of the filler:
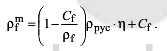
CCCM-formular
Here ρfm is the theoretical final density of the CCCM, g/cm3; Cf is the specific content of the filler in the original preform, g/cm3; ρf is the pycnometric density of the filler, g/cm3; ρpyc is the pycnometric density of the pyrocarbon matrix, g/c3; η is the ultimate possible level of filling cavities with pyrocarbon in the original preform during gas-phase densification. All of these parameters are easily calculated or determined by experiment. For example, the specific content of carbon fibers is calculated by dividing the mass of the preform by its volume, which is turn is determined from the geometric dimensions of the porous preform.