How carbon brushes work?
What is commutator film: you can see Fig.3-oxide layer
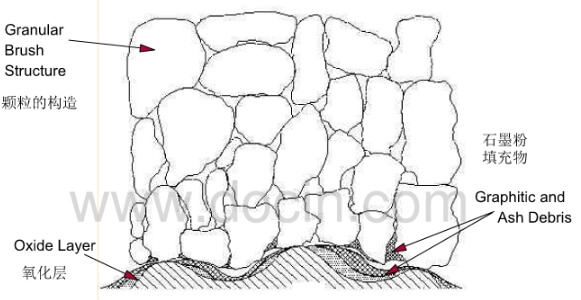
Fig.3-oxide layer
To enhance film formation, the commutator should be turned to a surface roughness of 35 to 60 uin. A film will not form properly if the commutator surface is too smooth.
A thin, uniform film having a brown/grey patina is desired.
- Overfilming- a thick, black film will increase contact drop and cause excess spaking and high electrical wear.
- Underfilming- a very thin or non-existent film will result in high frictional wear and may degrade commutation.
Base filming characteristics is normally controlled by the brush grade.
Contact drop vs current density:
What is brush wear?
What is electrical wear?
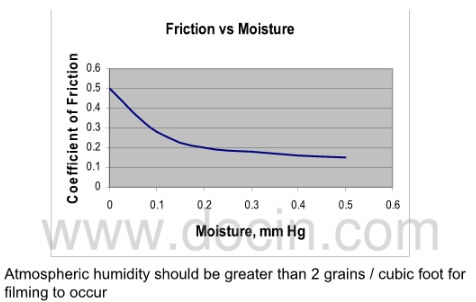
fig.4-friction vs moisture
- Voltage pulses cause rapid increases in temperature at the conducting spots in the brush.
- Small pieces of the brush are expelled, causing wear.
- Higher voltages cause an electric arc to form, causing extensive damage to brush and commutator. The contact spots are heated to 2500-3000°
Wear rate increases with current density.
Frictional wear:
- Shearing of graphite during sliding of brush face over commutator.
- Rapid during initial film formation.
- Greatly increased under some atmosphere and temperature conditions.
- Higher for high-metal content brushes having little graphite.
Both electrical and friction wear are increased by high commutator bar-to-bar profile and high TIR.
Effect of atmosphere on friction of graphite, see fig.4-friction vs moisture.
Low temperature:
Thermal stability of copper graphite brush is key to long life and stable performance.
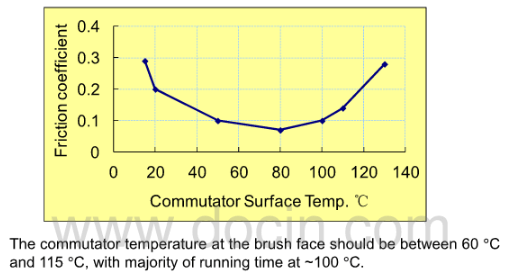
fig.5-brush face temperature
Under low temperature, it is difficult to build good film between brush and commutator surface, which caused fast mechanical friction; at the same time, the sparkle condition is bad.
Low temperature- low humidity- brush wear rapidly
Low temperature means low humidity, low humidity means the sub-pressure of water vapour is to low that the H2O molecular complete desorption from film.
High coefficient of friction- wear quickly.
High humidity- over filming.
related news /articles:
Carbon brush and brush materials-electrical carbon (1)-characteristics
New modernization technology— Carbon brush material
Carbon Brush | Electric Brush Guide by CFCCARBON LTD
Resin graphite material | carbon brush materials- manufacturer in China