Graphite electrodes for the production of electric-arc steel: As shown in table 5.11, the production of electrodes for steel and aluminum processing is the largest application of molded graphite, in terms of both tonnage and dollars. As mentioned in Sec. 1.1, electrodes are one of the original applications and have been manufactured with essentially the same process for almost a century.
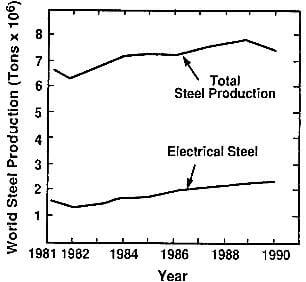
world production of steel.
The largest use of these electrodes is in the production of steel in electric-arc furnaces, mostly for the reclamation of ferrous scrap. These electrodes must have good electrical conductivity, good refractory properties, and low cost. They gradually erode in use and at times break altogether and must be replaced at regular intervals.
The worldwide production of steel is slowly increasing, but the production of electric-arc furnace steel is increasing at a more rapid rate. This rate reached 28% of total production in 1990 as shown in fig.5.11. The major producers by area are Europe, North America, and China.
The gradual increase in electric-arc steel production does not necessarily into a gradual increase in the tonnage of graphite electrodes. In fact the opposite is happening and the total consumption of graphite electrodes is decreasing due to a pronounced decrease in the consumption of graphite per ton of electric steel produced. In 1975, an average of 7.5kg of molded graphite was required to produce one ton of electric-arc steel. In 1990, this amount had dropped to 5kg. The downward trend is continuing.
This reduction is the result of two factors: (a) improvements of the properties of the graphite materials, particularly a considerable reduction of the thermal expansion and resulting increase in thermal-shock resistance, and (b) improvements in arc-furnace operating techniques.
Electrodes for Aluminum production: Aluminum is processed electrolytically and the production of the necessary electrodes is the second-largest application of molded graphite. The anodes are similar to those used in electric-arc steel production and are also manufactured from petroleum-coke filler and coal-tar pitch. The aluminum collects at the cathodes which are large blocks lining the electrolytic cell. These cathodes were originally made of baked carbon based on anthracite coal but, in recent years, have been upgraded and are now made of molded graphite from petroleum coke.
The world production of aluminum was estimated at 14.2-106 metric tons in 1990. The consumption of molded-graphite anode is approximately 400kg per metric ton of aluminum and the total estimated consumption worldwide is 5.68-106 metric tons.
Melting, smelting, and casting of metals:molded graphite has numerous applications in the processing of ferrous and non-ferrous metals and alloys such as copper, copper-nickel, brass, bronze, zinc, aluminum alloys, nickel and its alloys, precious metals, and grey and ductile irons. The wide variety of these applications is shown in the following partial list:
– Molds for centrifugal casting of brass and bronze bushings and sleeves
– Molds for pressure casting of steel slab and railroad-car wheels.
– Dies for continuous casting and extrusion of aluminum and other non-ferrous metals.
– Extrusion guides and run-out tables
– Hot-pressing molds and plungers
– Pumps for molten aluminum and zinc.
– Brazing fixtures
– Furnace linings.
– Sintering boats and trays.
The factors to consider in selecting a suitable grade of molded graphite for metal processing are: high thermal conductivity to reduce the thermal stresses; high hardness to reduce abrasive wear and improve the lifetime of the die; and high density, fine grain, and low porosity to minimize chemical attack by molten metals and by dissolved atomic oxygen.