The selection of the interlayer components was the fundamental step for the combustion joining. Taking the composition of the TiAl and the C/C substrates into consideration, the Ti-Al-C interlayer was selected to avoid introducing impurities into the joint. The heat generated by the self-sustaining interlayer reaction was the main energy needed to complete the interfacial joining. Therefore, it is necessary to ensure a self-sustaining reaction can occur for the given interlayer. The adiabatic temperature of the reaction provides a criterion for evaluating the suitability of a reaction system. In the Ti-Al-C system, the TiAl3 phase is the well-known first reaction product that causes the ignition of the self-sustaining reaction. After that, the reaction between Ti and C is activated to form TiC, which is the main exothermic reaction in the Ti-Al-C system. Because TiC is much more stable than the Ti-Al compounds from a thermodynamic view, Ti prefers to react with C in contrast to the as-synthesized TiAl3. The XRD pattern of the as-synthesized Ti-Al-C reaction products for this study is shown in Fig.2. The TiAl3 and TiC phases were detected in the reaction products. Only small amounts of unreacted Al are residual after the SHS reaction, which were derived from the exhaust of Ti via the reaction with C.Similarly, the reaction products only contained TiC and Al when combustion joining using a Ti-Al-C interlayer and a Ti/C molar ratio of 1.0 was performed.
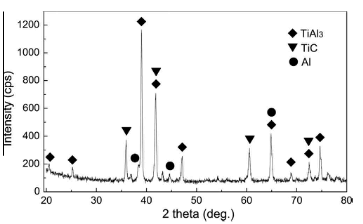
Fig.2 XRD pattern of the as-synthesized Ti-Al-C reaction products
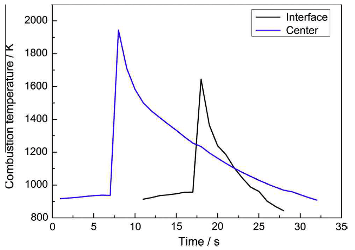
Fig.4 combustion temperature of the Ti-Al-C powder compact in the joint couples.
According to the reaction analysis for the Ti-Al-C system, the reaction can be defined as follows because only the final reaction products need to be considered for the thermodynamic calculation: (m+1)Ti+3Al+mC→ mTiC+TiAl3, where m is the molar ratio of TiC/TiAl3 in the products. Based on the reaction formula, the effect of the m value and the preheating temperature on the adiabatic temperature is shown in fig.3. The calculated results show that the adiabatic temperature obviously increases as the preheating temperature increases. In addition, the formation of TiC products is the main exothermic reaction in the Ti-Al-C system, which results in a drastic increase in the adiabatic temperature with an increasing m value. An adiabatic temperature of 2000K is often reported as the empirical lower limit for a self-sustaining combustion reaction. Additionally, the vaporization of the reaction products should also be avoided to decrease the porosity of the products. Therefore, the ideal adiabatic temperature for this reaction ranges from the critical temperature of 2000K to the vaporized temperature of Al. For the actual joining process, the joining couples were heated to the ignition temperature, which is the melting point of Al at 933K. Therefore, the temperature of 933K was the preferred preheating temperature for the selection of the reactant composition. Based on the above discussion, the ideal compositions of the reactants were determined from the calculation results.
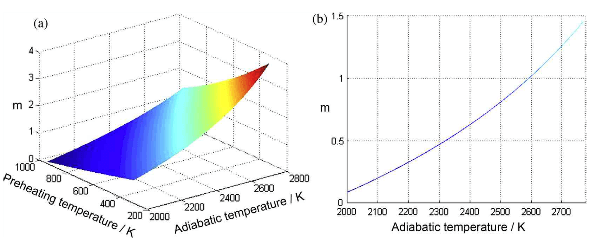
Fig.3-effect of m value and preheating tem on the T for the Ti-Al-C system (a) total effect, (b) cross section at a preheating tem of 933K.
Combustion temperature of the Ti-Al-C powder compact in the joint couples is given in Fig.4, the temperature rose abruptly after the self-sustaining reaction was ignited at approximately 930K. The peak combustion temperature in the sample center was approximately 1943K, which was higher than that near the interface due to the heat transfer to the substrate. The tested peak temperature was comparable with the results of a Ti-Al-C compact reported by Yeh et al. It was noted that the peak temperature near the interface was also much higher that the melting point of the Ag-Cu-Ti filler metal, which ensured sufficient wetting and reaction of the filler metal.
Because the exothermic reaction was ignited at the melting point of Al, several undesirable additional reactions are likely to occur. If the as-synthesized TiC contacted with liquid Al, the reactions: 4Al(l)+3TiC(s)→ Al4C3(s)+3Ti(l) or 12Al(l)+3TiC(s)→ Al4C3(s)+3TiAl3()l are possible. If the Al4C3 remained in the final products, it will deteriorate the joint due to the bruttle and hygroscopic properties, Fortunately, the reaction between Al(l) and TiC(s) to form Al4C3 only can occur at a temperature <1085K. At a high temperature, the TiC(s) is more stable in the Al melt, and Al4C3 can react with Ti or TiAl3 to form TiC. For the combustion joining process in this study, when the system was heated to the melting point of Al, the SHS reaction was ignited and the temperature increased rapidly. Therefore, only small amounts of Al4C3 were formed, and then they transferred to the TiC, thus, the additional reaction between Al(l) and TiC(s) will not influence the microstructure and bond strength significantly.
Due to the unavoidable oxidation of the Ti powders, another additional reaction of 3TiO2+3D=(4+x)Al →3TiC+2Al2O3+xAl will occur. Therefore, the effect of this reaction on the microstructure and bond strength of the joint needs to be discussed. In the reaction products, TiC is the desired reaction product and Al will take part in the following reaction. So only the formation of Al2O3 will play an influence on the joint microstructure. The Ti-containing melt both in the original reaction system and in the Au-Cu-Ti filler metal exhibits a good wettability on the Al2O2, which led to no additional defects derived from the existence of Al2O3. In addition, from the XRD pattern of the products shown in Fig.2, no Al2O3 is less than 5 wt.%. therefore, the small amounts of Al2O3 will not affect the microstructure. On the other hand, from the thermodynamic calculation, this reaction is also highly exothermic and self-sustaining when the content of Al is not excessive, which is the case for this study because most of Al was consumed by Ti or C. Therefore the above given reaction will not decrease the reaction heat and will only have a slight effect on the interfacial joining, especially on the C/C composite joining by the Ag-Cu-Ti filler metal. In addition, the TiC-Al2O3-Al composites were manufactured according to this reaction, and the products exhibited excellent properties. Thus, the reaction between TiO2-Al-C to form the TiC-Al2O3-based composites will not degrade the properties of the joint.