Wet-molded integral Rayon graphite felt insulation barrel-crystal growing furnace
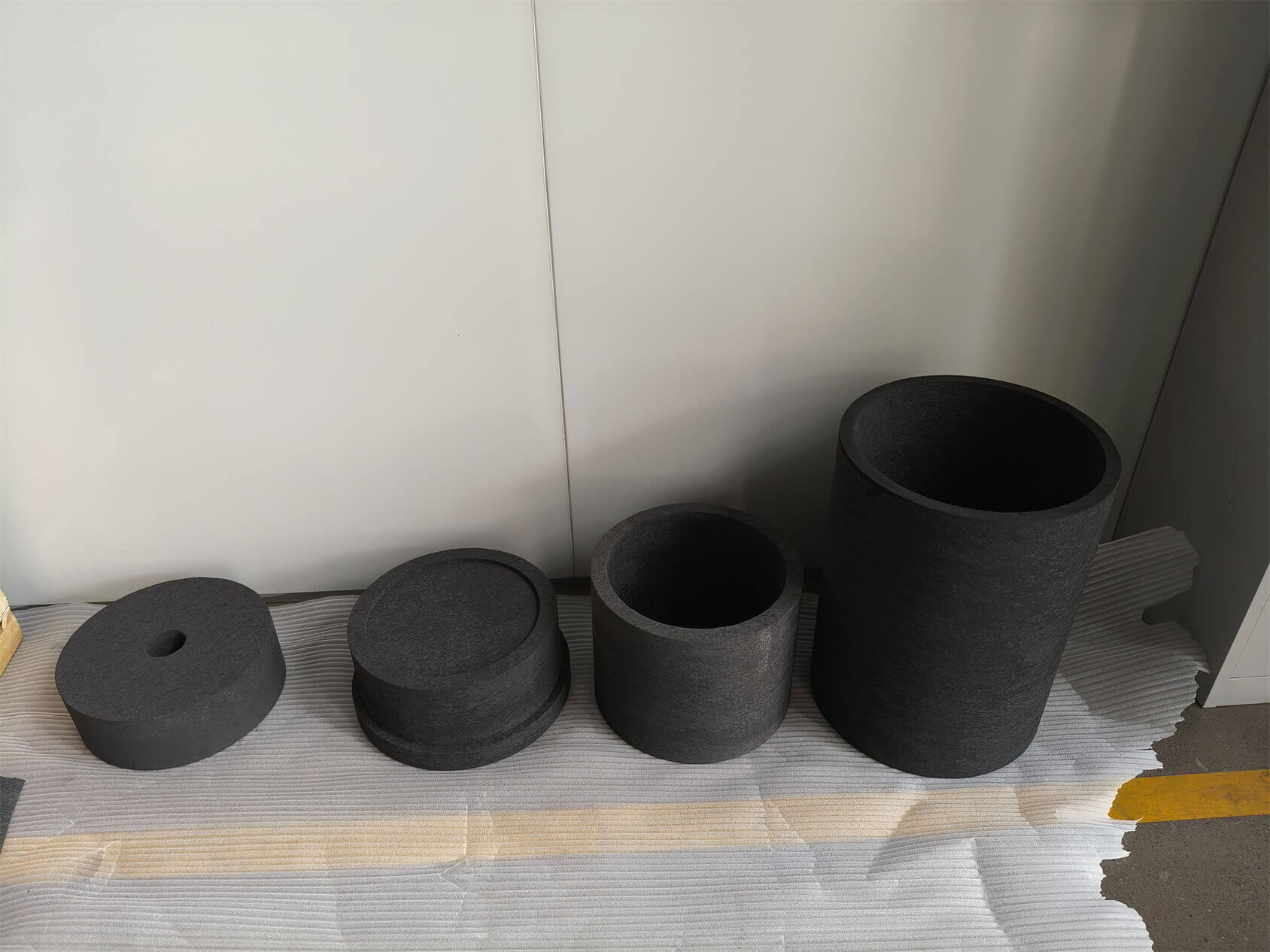
Wet-formed graphite felt is a graphite fiber reinforced material prepared by a wet process. It has the characteristics of high thermal conductivity, high temperature resistance, and corrosion resistance. It is mainly used in the following fields:
Main application areas:Insulation materials for single crystal silicon smelting furnaces
As a key material in the production of single crystal silicon, wet-formed graphite felt can effectively isolate high-temperature areas, reduce heat conduction, and improve process efficiency.
Insulation and heat insulation materials in various crystal growth furnaces…
Detailed description
Keywords: graphite felt, wet forming, integral felt, single crystal furnace, crystal growing furnace, insulation material, Rayon-based graphite felt, manufacturer
Wet-molded felt is a material formed by compounding carbon fiber and resin through a wet process, which has the following significant advantages:
I. Main performance advantages
Corrosion resistance
The surface of wet-molded felt forms a uniform resin coating, which can effectively resist the erosion of corrosive media such as acids, alkalis, and salts, and is suitable for special environments such as chemical industry and ocean.
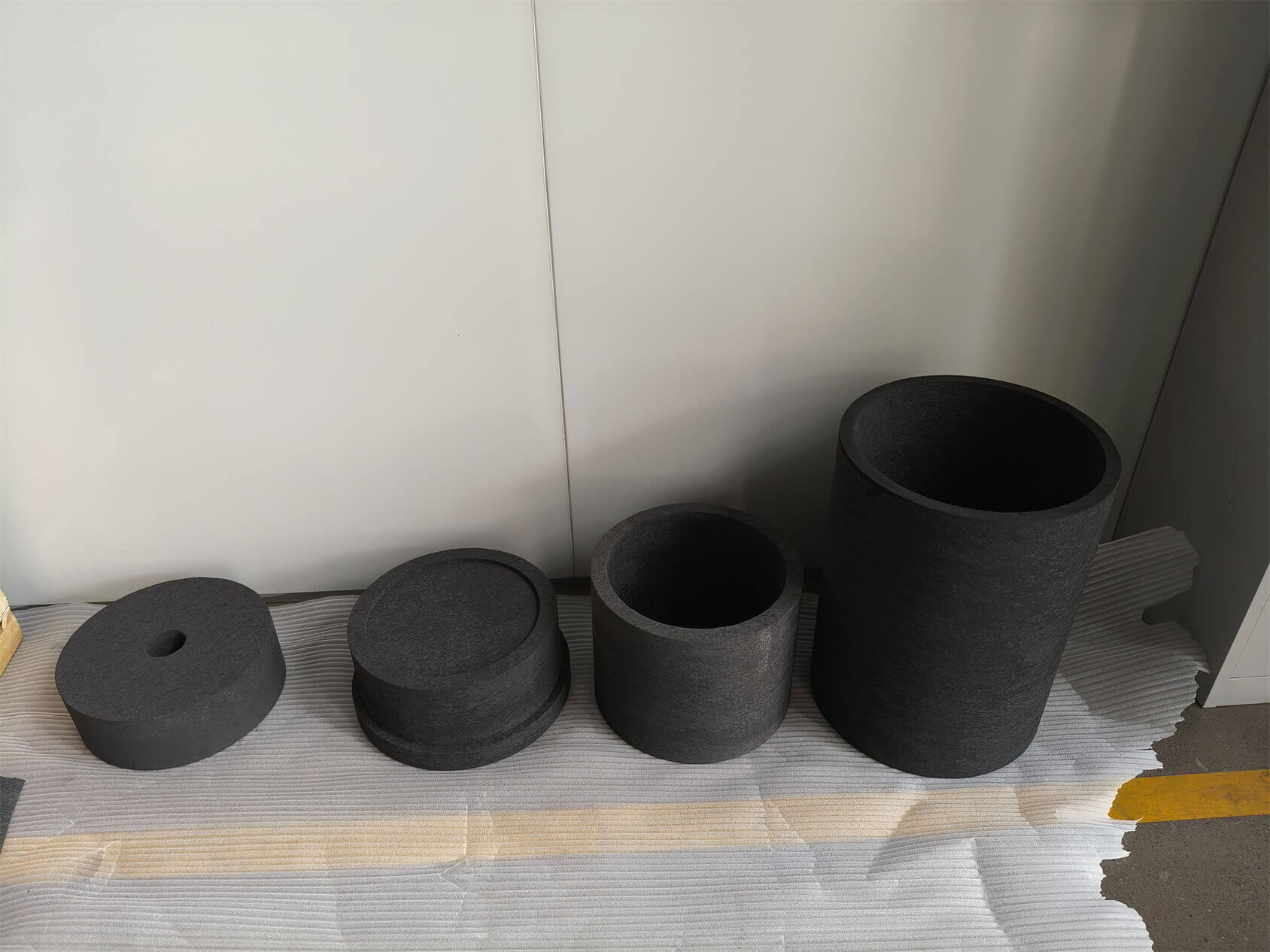
crystal growing furnace-graphite felt insulation barrel
High temperature resistance
The high temperature resistant resin system is adopted, and the working temperature range is wide, which can meet the needs of aerospace, high temperature equipment and other fields.
Insulation and sound insulation effect
The porous structure design reduces heat conduction, and the material itself blocks sound propagation, which is suitable for building sound insulation and insulation systems.
Lightweight
Compared with traditional composite materials, wet-molded felt has a lower density (80-100kg/m³ for dry method and 100-130kg/m³ for wet method), which reduces the structural load.
II. Process and performance optimization
Dimensional stability
The wet process ensures uniform fiber distribution, high product dimensional stability, and reduces deformation caused by environmental changes.
Surface flatness
The surface finish is improved through the stitching process, which is convenient for subsequent processing and decoration, especially suitable for scenes with high surface quality requirements such as kitchenware and building templates.
Customizability
The resin formula and fiber content can be adjusted to meet different performance requirements, such as enhancing acid and alkali resistance or high temperature resistance.
Wet-molded graphite felt is a composite material prepared by wet impregnation. Its advantages and disadvantages are as follows:
1. Advantages
Strong corrosion resistance
During the wet molding process, graphite fibers are combined with the matrix material through chemical bonding to form a dense microstructure, which significantly improves corrosion resistance and is suitable for corrosive environments such as chemical and environmental protection.
Flexible process
Graphite felts with different properties can be customized by adjusting the wet impregnation liquid formula and process parameters to meet diverse needs.
Low equipment investment
Compared with dry molding, wet equipment is simple, suitable for small and medium-sized production, and reduces initial investment costs.
2. Disadvantages
High cost
Wet production requires the use of chemical solvents and special equipment, and the subsequent processing is complicated, resulting in an overall cost higher than the dry process.
Long drying time
It takes a long time to dry, usually several days to a week, which affects production efficiency.
Low product purity
Impurities may be introduced during the wet impregnation process, and the surface treatment process may affect the density of the felt layer, resulting in a purity slightly inferior to that of dry products.
Size limitation
Due to the limitations of equipment volume and operating space, wet molding is difficult to produce oversized graphite felt.
III. Wet molding graphite felt is a graphite fiber reinforced material prepared by a wet process. It has the characteristics of high thermal conductivity, high temperature resistance, and corrosion resistance. It is mainly used in the following fields:
1. Main application areas
Insulation materials for single crystal silicon smelting furnaces
As a key material in the production of single crystal silicon, wet molding graphite felt can effectively isolate high temperature areas, reduce heat conduction, and improve process efficiency.
Insulation material in various crystal growth furnaces
As a good insulation material, wet-formed graphite felt is used in various crystal growth furnaces as insulation and heat insulation materials, playing a very critical role. It is also a key insulation material in the semiconductor industry.
Chemical industry filter material
Its high purity chemical stability makes it suitable for filtering highly corrosive chemical reagents, which can prevent chemical penetration and ensure process safety.
High temperature environment sealing material
Under high temperature or high pressure scenarios, wet-formed graphite felt can provide reliable sealing, avoid medium leakage, and extend equipment life.
2. Other potential uses
Thermal isolation and insulation: Using its excellent insulation performance, it can be applied to the heat dissipation system of nuclear reactors, high-temperature furnaces and other equipment.
Corrosion-resistant equipment protection: As an anti-corrosion coating material, it can protect metal equipment from corrosive media such as acids and alkalis.
Environmental protection: Some products can reduce energy consumption through surface treatment, which is in line with the trend of green industry.
Energy storage field: In high-temperature scenarios, the high-temperature resistance (up to 3000℃) and chemical stability of graphite felt make it a key material in molten salt energy storage, thermoelectric energy storage and other fields.
Safe energy storage: Some studies explore the application of graphite felt in high-safety energy storage systems such as lithium-sulfur batteries, using its inert properties to prevent direct contact between positive and negative electrodes.
IV. Process innovation and improvement
The new wet-process felt optimizes the wire drawing process by adding impregnation agents, improves fiber dispersion and mechanical properties, and reduces subsequent processing costs.
In summary, wet-process felt has broad application prospects in many fields due to its comprehensive performance advantages.
IV. Summary and suggestions
Wet-processed graphite felt is suitable for projects with high corrosion resistance requirements and limited budgets, but the cost and production cycle need to be weighed. For scenarios with strict purity requirements, it is recommended to combine dry methods or other advanced technologies to optimize the process.
V. Technical advantages and characteristics of wet-processed integral graphite felt produced by our company
High thermal conductivity: significantly reduce thermal resistance and improve thermal conduction efficiency3.
High temperature resistance: can work stably above 3000℃ and adapt to extreme working conditions.
Chemical stability: resistant to corrosive substances such as acids, alkalis, and salts.
The wet forming process can customize the shape and density through molding or extrusion combined with high-temperature sintering. The product can be purified according to customer requirements to meet different application requirements.
VI. Performance indicators of wet-formed integral graphite felt produced by our company:
See the properties/data sheet at this link: https://www.cfccarbon.com/wp-content/uploads/2025/03/03-Rigidgraphitefeltboard-ENGLISH.pdf