Yarns and rovings are linear fibrous assemblies composed of discrete or continuous fibers. The basic differences between rovings and yarns are listed bellow:
- Rovings are large fiber bundles with little or no twist.
- Yarns are finer bundles with some twist.
Yarns that are composed of discrete fibers are called staple yarns; yarns having continuous fibers are continuous-filament yarns. The majority of high-performance yarns are continuous-filament yarns having single or multiple strands. Figure 2 bellow shows the geometric features of filament yarns.
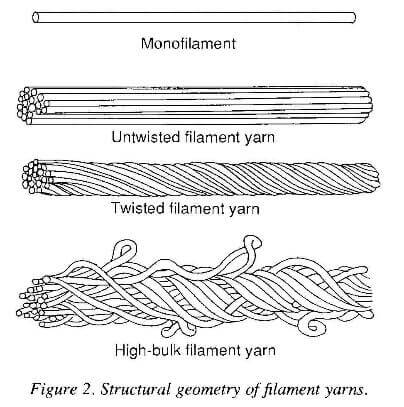
structural geometry of filament yarns
The technology for converting short fibers into yarn assemblies is well established. For high-modulus fibers that exist in staple from, special yarn formation techniques have been developed. For example, researchers are growing long SiC whiskers for spinning into staple yarns. Similar methods may be applicable for the vapor-grown carbon fibers developed at the Laboratory. Through proper selection of whisker length and yarn twist level, the pore structure and mechanical properties of the staple yarn can be engineered for weaving into 2D or 3D fabrics for carbon-carbon composite.
Motivated by the need of finer carbon yarns, Heltra, a division of Courtaulds, has also developed a staple yarn formation method using a stretch breaking process. Compensating for the inevitable reduction in tensile strength, the protruded fibers on the transverse direction of the staple yarns can potentially improve the through-the-thickness strength and shear resistance and also the toughness of the CC composite. The improvement in properties is derived from the subtle interlocking of the protruding fiber creating a network of in-plane and out-of-plane crack arrestors. An example of a yarn manufacturing process and produces protruding fibers in the transverse direction is the family of hispiduous yarns created by chenille process.
We are manufacturer of carbon carbon composite | C/C composite in china, with stable and reliable quality. Our products: 2D,2.5D,3D,4D carbon composite, with density from 1.40-1.95g/cm3, with CVD, CVI processing, or pitch based carbon composite. also, we produce carbon ceramic composite material and products.